There are numerous factors to consider when it comes to clean rooms for medical devices. Clean room injection molding is a technology that allows a corporation to make complicated plastic products without having to worry about the detrimental effects of germs and other impurities. The cleanroom is carefully constructed to keep a sterile atmosphere, allowing the company to produce high-quality items without fear of contamination.
Another thing to consider when looking for a medical molding firm is partnering with a supplier with the experience, resources, and ability to help satisfy the consumer’s specific needs. When looking for a manufacturer, learn and validate their expertise in the medical molding business, including their ability to meet one’s particular needs.
Inquire about their present partnerships with other companies and their experience dealing with manufacturers. When dealing with a medical molding firm, it is critical to consider their licensing. It’s important to check check the supplier the consumer choose if has the necessary licenses for the jurisdiction in which they will work.
Before making a commitment, it is critical to confirm this information. Furthermore, medical molding company – Seaskymedical provides these standards and qualities of their medical room and its medical device.
This article will introduce the benefits and importance of clean room molding and other information about medical injection. So, let’s dive in.
What Is Clean Room Injection Molding?
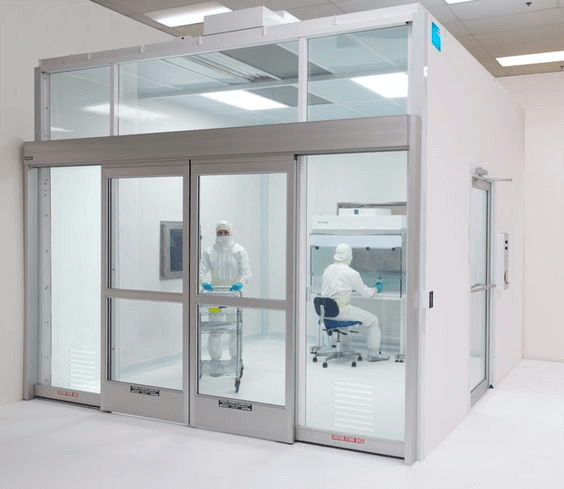
Cleanroom molding is the technique part producing plastic parts in a controlled environment to limit the danger of particle contamination. Several businesses require specialized components fabricated in a cleanroom environment for increased safety and precaution.
It is most typically utilized in medical injection molding and the manufacture of other medical products.
Machines inside cleanrooms must be checked and cleaned regularly. Floors, walls, tools, and workstations must be kept sanitary and sterile during production and thoroughly cleaned afterwards. Cleanrooms must also be adequately ventilated with filtered air.
Cleanroom molding employees are required to wear protective clothing such as hairnets, gowns, gloves, and shoe covers. Any specific clothing worn inside the cleanroom is not permitted to be worn outside the facility. A separate clean gowning space is usually provided. In addition, Seaskymedical have an isolated area that meets the clean room injection molding requirements.
The process of maintaining and controlling clean room protocol and clean room certification and accreditation for medical injection molding is extensive. To stay in compliance, clean room injection molders must pay close attention to several elements, including
Hygiene
Cleanroom settings decrease contaminants and dust particles daily to avoid impacting product quality and reliability. This is crucial for companies who wish to develop trust in medical items by guaranteeing that their standards meet all health and safety criteria.
Increase the Probability of an Injection Machine
Airborne contamination is a major problem in the medical injection sector. The cleanroom system addresses this by carefully controlling air flow rates and direction and compression, temperature, and humidity levels, thereby boosting machine life and performance.
Contamination
The sterile injection molding in a clean room eliminates contamination. This is by using positive pressure to prevent non-filtered air from flowing back into the cleanroom via the exhaust terminals. Ensuring that air pollutants do not accumulate on small components, affecting their capacity to function.
High Clean Room Performance
The benefits of static control humidity and air pressure control, as well as the Latex floor, clean rooms have a good performance for the medical injection mold. It has a good cleaning ability and does not readily absorb dust.
Why Clean Room Molding Is So Important
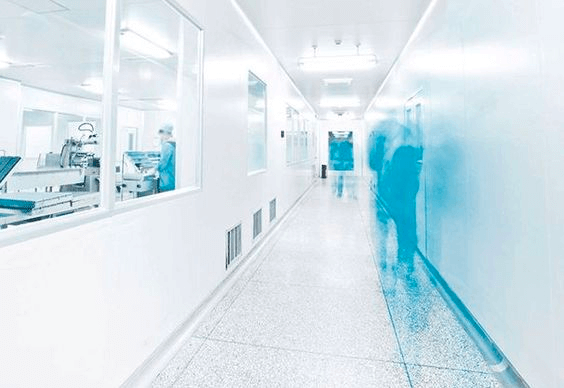
In order to keep the surrounding area sanitary, it is essential to manufacture products using clean room molding. Clean room molding is an example of a manufacturing process that takes place in a controlled environment. This ensures that the space is sanitary and devoid of any harmful substances. When manufactured goods are molded in a clean room, it helps to ensure they are free of contamination.
Utilizing molding produced in a clean room comes with several advantages. It is of assistance in the process of establishing a sterile environment. This is of utmost significance in regard to medical equipment. Another advantage is that it lessens the likelihood of contamination spreading from one area to another.
Cross-contamination is when one product becomes tainted as a result of another product becoming tainted. If the products are not kept in different locations throughout the production process, this is possible. By separating different types of products from one another, clean room molding lowers the likelihood of contamination spreading.
Molding in a clean space presents a wide variety of difficulties. One potential drawback is that the cost can be high. This is because the essential tools and components could come at a high price. In addition, maintaining a clean and sanitary working environment might be challenging.
This is because a wide number of causes can be responsible for the contamination that occurs. If the environment is not thoroughly monitored, potentially harmful substances could make their way into the space.
Clean Room Classification for Medical Device Injection Molding
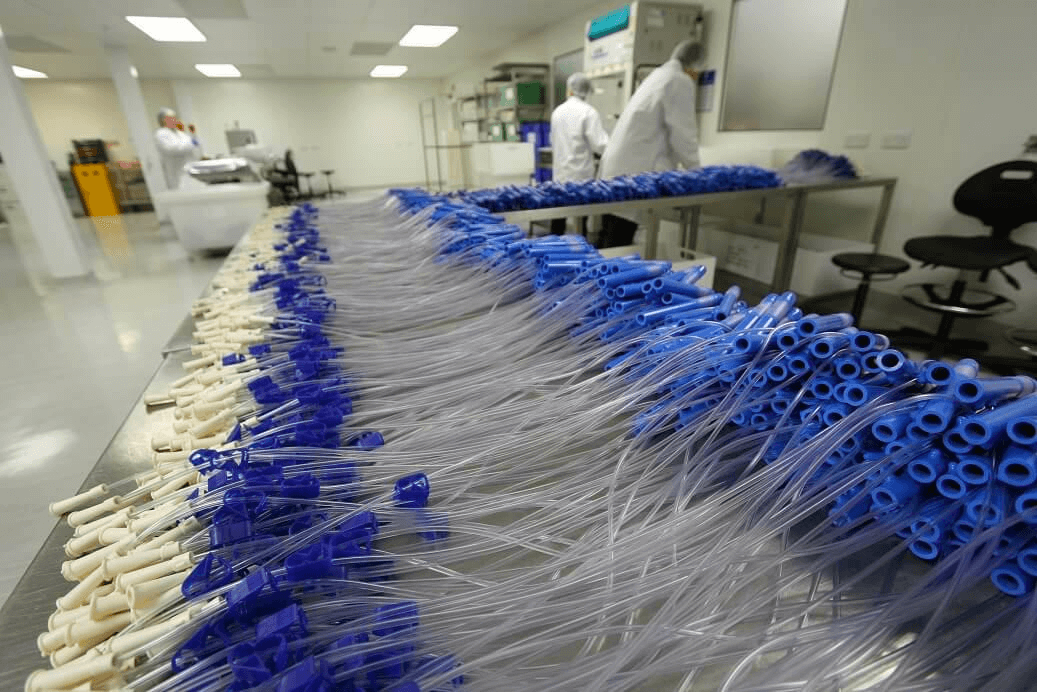
Medical device injection molding, it must be kept as clean as possible when producing a plastic part, such as an implantable medical device. A sterile environment is required for the production of such a part. This type of environment is known as a clean room.
A clean room is a controlled environment in which the amount of airborne contaminants per unit volume, such as dust and other airborne germs, is reduced to reduce the possibility of contamination. These particles are filtered using a High-Efficiency Particle Air (HEPA) filter, which filters the air before entering the cleanroom and is changed multiple times per hour, according to the cleanroom class defined by the International Standard Organization (ISO) 14644-1.
Clean rooms are kept under positive pressure to allow particles to escape from the cleanest to the least clean section in order to preserve a product free of pollutants. However, some cleanrooms, such as quarantine stations and chemical analysis facilities, are kept under negative pressure to keep nothing out of the cleanroom.
Plastic parts are produced in a separate room that has been adjusted to decrease the possibility of contamination from dust or other particles. This is referred to as cleanroom molding. Parts must frequently be created in sterile medical, pharmaceutical, and biotechnology environments.
Before getting into cleanroom molding, it is critical to grasp the distinction between an ISO 7 and an ISO 8 cleanroom.
Clean rooms are classified into nine sorts, or classes, with Class 1 being the most sterile and Class 9 being the least sanitary. Most plastic injection molding in a cleanroom setting occurs in Class 7 or Class 8 cleanroom.
A more sterile cleanroom environment may be required for the plastic item with a very low tolerance for foreign object debris, such as a lens used in a thermal imaging weapon scope. Understand more what is the difference between ISO 7 and ISO 8 clean room for plastic injection molding as follows:
ISO 7 Cleanrooms for Plastic Injection Molding
A Class 7 Cleanroom is a contained injection molding environment with solid walls that separates it from the rest of the production floor. Air is constantly changed, cleaned, and metered to maintain ISO 14644-1 compliance for particulates.
- There can be 352,000 particulates >= .5 micrometer per cubic meter of air
- There can be 83,200 particulates >= 1 micrometer per cubic meter of air
- There can be 2,930 particulates >= 5 micrometers per cubic meter of air
In order to retain its classification, a third-party agency inspects and calibrates the Class 7 Cleanroom regularly (either annually or biannually, depending on the facility).
ISO 8 Cleanrooms for Plastic Injection Molding
Class 8 Cleanroom requirements are less stringent than Class 7 Cleanroom requirements. Molding equipment is surrounded by movable tenting on the shop floor of a Class 8 Cleanroom. To meet the ISO 14644-1 particle standards, a positive airflow is maintained, as in Class 7.
- There can be 3,520,000 particulates >= .5 micrometers per cubic meter of air
- There can be 832,000 particulates >= 1 micrometer per cubic meter of air
- There can be 29,300 particulates >= 5 micrometers per cubic meter of air
Industries That Require Clean Room Molding Capabilities
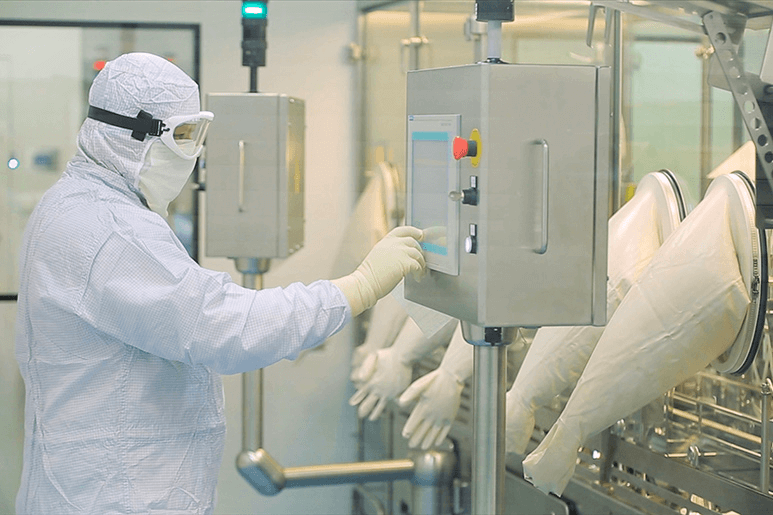
1. Semiconductor Industry
The semiconductor industry has relied on clean room molding to maintain the quality of its products since its debut. Indeed, the sector has created cleanliness standards that are among the most stringent in the world. To meet these standards, semiconductor manufacturers must have access to specialized equipment and personnel.
One of the most difficult challenges in semiconductor production is controlling the presence of particles. Particulate matter can come from various sources, including human skin cells, hair, clothing fibres, and dust. Because even the tiniest particle might contaminate a semiconductor device, manufacturers must adhere to strict cleanliness standards.
Clean room molding processes are used by semiconductor manufacturers to prevent particle contamination. These tactics include using HEPA filters to remove contaminants from the air, laminar flow hoods to keep work areas clean, and specific gowning procedures to avoid introducing contaminants into the work environment.
Molding in a clean room is essential in the semiconductor manufacturing process. Producers may use these strategies to ensure that their products are of the highest quality and free of faults.
2. Solar Panel Industry
The solar panel sector is one of the fastest expanding in the world. As the demand for solar panels grows, clean room molding capabilities will be necessary.
Molding in a clean atmosphere allows manufacturers to make solar panels of consistent quality and with fewer faults. A clean room prevents dust and other contaminants from touching solar panels during production. A higher-quality product is less likely to cause installation or operation troubles.
There are numerous advantages to using clean room molding for solar panel production:
- improved panel quality – by preventing impurities from coming into contact with the panels during production, the end product’s quality is improved.
- decrease manufacturing costs – because the end product has fewer faults, less waste and rework are required, lowering manufacturing costs.
- shorter production cycle – the clean room environment speeds up manufacturing, allowing businesses to keep up with demand.
Producers can boost customer satisfaction and brand loyalty by providing a higher-quality products. The solar panel industry is still in its infancy, and only a few firms have cleanroom molding capabilities.
3. Hard Disk Drive Industry
The hard disk drive industry is evolving and becoming more sophisticated. The hard disk drive business requires clean room molding skills to meet the ever-increasing expectations of customers. This means that the hard disk drive manufacturing process must be able to take place in a sterile and contamination-free environment. Manufacturing high-quality hard drives would be exceedingly difficult, if not impossible, without these clean room molding capabilities.
One of the key benefits of using clean room molding is that it offers continuous quality control. Minor changes to the manufacturing process (such as installing a new component or replacing an existing one) must be documented and thoroughly tested before being implemented on the production line. This helps to avoid unexpected problems and results in a cleaner, more trustworthy product.
Another benefit of clean room molding is that it allows for innovative manufacturing techniques. It is possible to produce components that cannot be made using traditional methods utilizing 3D printing, for example. This is possible because the production line is free of contaminants and can thus operate at high speeds.
Manufacturing high-quality hard disk drives would be tough without clean room molding.
4. Optical Fiber Manufacturing Industry
Molding in a Clean Room The optical fibre manufacturing sector requires capabilities to ensure high-quality products. Clean Room Molding is a technique for producing precision optical components by replicating an original component’s dimensions. It is a critical production phase that demands specific methods and equipment to ensure the final product’s quality and precision.
Clean Room Molding is an important stage in the manufacturing of optical precision components. By reproducing the original proportions, the technique aids in the manufacture of accurate parts. Special procedures and equipment are necessary to ensure the quality and precision of the finished product.
The Optical Fiber Manufacturing Industry uses Clean Room Molding to create precision optics components. Clean Room Molding is a technique for producing exact pieces by replicating the dimensions of a larger object. It is a critical production phase that demands specific methods and equipment to ensure the final product’s quality and precision.
Precision optical components would be difficult to build without Clean Room Molding. Clean Room Molding is a critical stage in the production of optical components. By reproducing the original proportions, the technique aids in the manufacture of accurate parts. Special procedures and equipment are required to ensure the quality and precision of the finished product.
5. LCD and LED Manufacturing Industry
The LCD and LED Manufacturing Industry are always looking for ways to improve the quality and speed of its products. To accomplish this, they constantly look for new approaches and technology to improve their products. Clean room molding is one of these ways. Clean room molding is the process of producing LCD and LED displays using specially designed molds. This molding is done in a sterile environment, which is critical for assuring the highest product quality.
In the LCD and LED manufacturing industries, clean room molding is a critical process. It allows for the production of high-quality displays far faster than traditional approaches. This is because clean room molding does not require using hazardous chemicals or materials. This ensures the safety of both the workers and the finished product.
Furthermore, clean room molding is more exact than traditional approaches. This is because precise measurements may be taken as the display is formed. In general, this leads to considerably superior products.
Clean room molding is critical in LCD and LED production processes. It allows for the production of high-quality displays far faster than traditional approaches.
6. Biomedical Implants and Devices Industry
Biomedical implants and devices have various medical applications, from primary prosthetic implants to complex life-saving systems. The production procedure for these devices is highly regulated and utilizes clean room molding to ensure the quality and safety of the end product.
Molding takes place in a clean room in an environment free of contaminants and particles that could potentially affect the delicate components of biomedical implants and devices. Special equipment and processes must be used to create a clean room molding environment.
Molding in a clean space starts with preparing the molding area. This entails thoroughly cleaning the room and removing any potential sources of contamination. Molding can begin once the space has been prepared.
Molding takes place in a specific chamber designed to maintain a controlled atmosphere. The room is then filled with a molding material, such as plastic or metal, and the implant or device is shaped appropriately. After the molding process, the implant or device is removed from the room and cooled.
After cooling, the implant or gadget is checked for faults and quality control. If any issues are detected, the device is usually removed and the procedure must be restarted.
7. Food and Beverage Industry
The food and beverage industry is always looking for new ways to save costs and increase productivity. Many firms have implemented carefully controlled food production processes in response to the global trend toward healthier eating. This needs stringent compliance with food manufacturing safety regulations.
To meet these standards, organizations must have molds that are entirely free of contamination. Even the smallest mold spores might cause a hazardous condition. For this reason, food and beverage companies require clean room molding capabilities.
A clean room molding capacity entails the flawless manufacture of complex items, such as food containers and packaging, using various materials and procedures. The method begins with the creation of a sterile, contained environment. The production equipment is then moved inside the clean room.
To ensure a perfect finished product, each stage of the manufacturing process must be strictly regulated. This includes the use of specialized equipment and clean room molding methods. Food is manufactured using the capacity to mold in a clean environment.
8. Pharmaceutical Manufacturing Industry
The pharmaceutical production business is rapidly expanding. This is because there is a demand for new, higher-quality drugs. Furthermore, the cost of these treatments continues to climb. As a result, the pharmaceutical production industry is working to improve its processes.
The pharmaceutical manufacturing sector seeks to enhance its methods by adopting clean room molding. This is because clean room molding can help to produce high-quality medications. Furthermore, clean room molding decreases the possibility of infection. Moreover, it aids in ensuring that drugs made are safe for consumer use.
Plastic components are created in a controlled environment. During clean room molding and this is performed by the use of molding machines. These devices are used to produce contaminant-free plastic components. Molding in a clean room involves several steps. The production technique must first be regulated. This means that all materials used in the manufacturing process must be treated with care. Second, the equipment’s operating environment must be clean. This means that no contaminants can enter the machinery or parts being produced.
9. Semiconductor Industry
Specific handling techniques must be used to prevent dust and other contaminants from coming into touch with the components during semiconductor production. This is especially important given semiconductors’ susceptibility to contamination. Semiconductor contamination can cause a range of electrical and mechanical issues.
Molding in a clean room makes the small components necessary for semiconductor production. Molding in a clean room is a highly specialized industrial operation requiring stringent environmental controls. This comprises the application of specific materials and equipment.
Clean room molding capabilities are required by semiconductor manufacturers to make precise and trustworthy components. Businesses can reduce contamination-related difficulties by using clean room molding.
10. Biotechnology Industry
Biotechnology is one of the world’s most innovative and fastest-growing industries. To be competitive, biotechnology companies require cleanroom molding skills. This mandates that the equipment used to create molds and castings be clean and well-maintained. Contamination can spread quickly in a clean room, causing production delays or even product recalls.
To ensure cleanliness, all materials entering and exiting the clean room must be thoroughly cleansed and sterilized. Molds are manufactured in a clean room using compressed air using molding machines. Any particles introduced into the air during the production process must be eliminated using filters or traps. Contaminants that may enter the room in this manner include bacteria, dust, and metal particles.
Everyone in the clean room must follow strict safety requirements to keep the machinery clean. All surfaces and equipment must be thoroughly cleaned and disinfected after each usage. Furthermore, all personnel working in the clean room must wear safety equipment. This includes eye protection, gowns, and masks.
The air quality in the clean room must be examined frequently to maintain a sterile atmosphere. If pollution is found, the air in the room must be replaced with fresh air.
Environmental Control for Injection Molding in Clean Room

ISO 7 and ISO 8 cleanrooms require low-risk situations, such as general surgery, gynecology, patient preparation/awakening corridors, critical care and resuscitation, and so on. Many checks should be done to assure environmental control, including verification of instrument calibrations, treatment system adjustment, airflow, air unidirectionality (when there is a filtering plenum), noise, and the smoke test.
Take into account the following aspects of the desired environment:
To ensure air quality, Class 7 and 8 cleanrooms use positive airflow to maintain clean air and a small number of particles.
Electric machinery, rather than hydraulic engines, should be used in most cleanroom conditions. The number of particles in the air would be reduced as a result.
Requirements for Coverage:
Engineers and operators must be completely covered when entering an ISO 7 cleanroom. Shoe covers, full-body garments, and low-cost covers are examples. Coverage requirements may be stricter in eighth grade.
Packaging Restrictions: Cardboard and plastic-coated plastic packaging are common in cleanrooms. Particle-generating packaging, such as some corrugated board materials, is not permitted in cleanrooms.
What Are the Clean Room Injection Molding Requirements
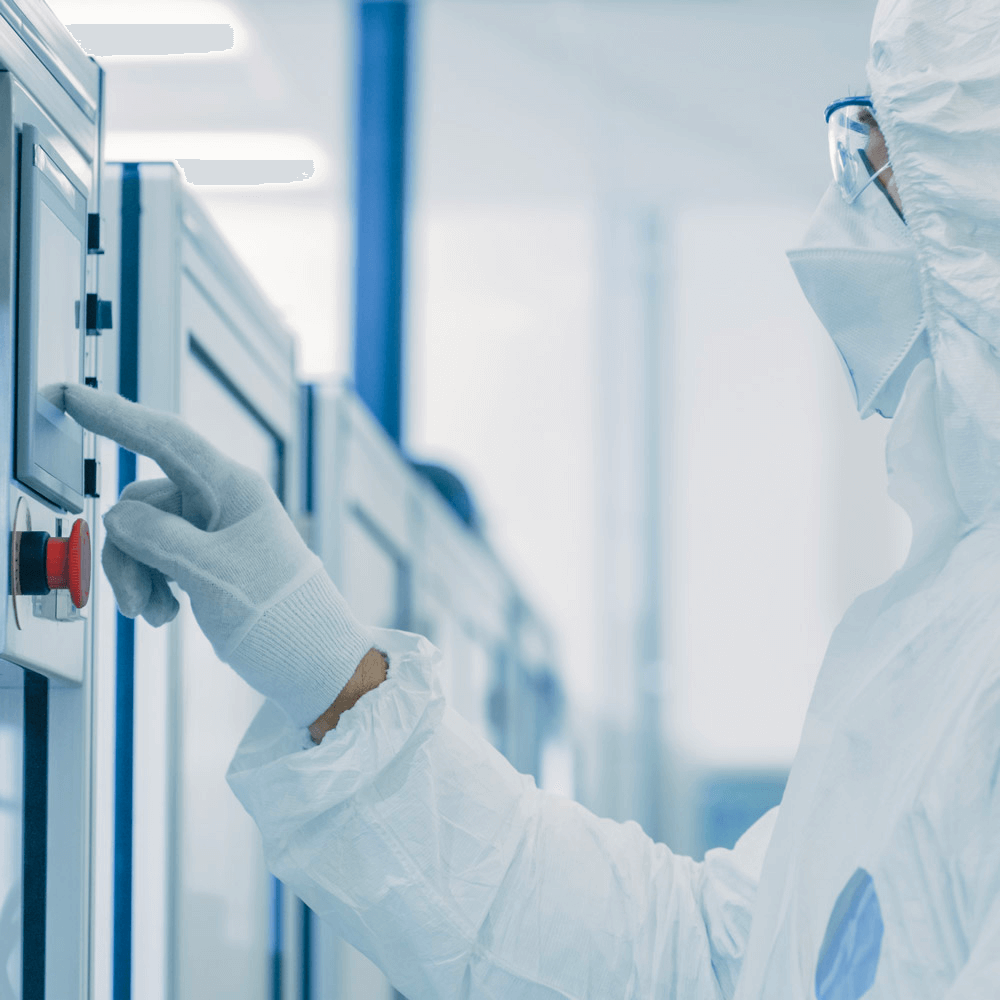
Molding requirements for a clean room differ from those of a typical injection molding floor. This section explains the basic requirements for an injection molding clean room.
Loading System
All components entering the cleanroom, save raw materials, must pass through a negative pressure chamber. All dust particles will be removed from this location before entry to the cleanroom is granted.
Finished goods manufactured and sealed in the cleanroom are also transported using this loading system.
Material Drying Equipment
Material drying equipment is kept outside of the clean room. It is sealed to keep contamination out of the cleanroom and requires little to no maintenance.
Because loading the dryers, testing the material, and removing it from the cleanroom pose contamination risks, the material drying equipment must be stored outside. As a result, the complete system is housed in a safe environment outside.
The drying equipment is linked to the feeding apparatus. Furthermore, an annual maintenance inspection is undertaken to ensure that there is almost no danger of contamination within the cleanroom.
Cooler System
Water must be used to cool injection molding machines when they are in use. The chiller that brings water to the proper temperature is located outside the cleanroom. Because the chiller device draws air from outside and warms it, it is ideal to be out of a cleanroom environment. As a result, only pipes delivering cold or hot water are meant to fit.
The cold water enters the cleanroom, cools the machine or mold, and then the chilled, warm water exits the cleanroom. The pipes allow for chilling without putting contamination at risk.
Feeding System
In most cases, an injection machine can be fed by hand, especially for very small production runs or sampling activities. In most high-volume production, a feeder is attached to the machine and sucks plastic into the machine. The feeder is frequently in close proximity to the material dryers.
Because dryers are prohibited in a cleanroom, the plastic resin must be transferred to the machines via pipes. The pipes will transfer the material directly into the machine from the ceiling.
Electric vs Hydraulic Machines
In clean rooms, electric machines often replace hydraulic machines to prevent the development of airborne particles. This is because hydraulic machines have fewer motors, joints, gear mechanisms, and subsystems.
On the other hand, electric machines lack the hydraulic system’s hoses, filters, tubes, and valves. As a result, electric machines reduce the possibility of contamination. This allows for a contamination-free injection machine loading technique.
Positive Pressure Airflow
Positive Pressure shows that the air pressure within the clean room is higher than the outside air pressure. A positive pressure air flow is created by pumping clean, filtered air from the ceiling into the cleanroom.
When keeping contaminants from entering the cleanroom is a primary priority, positive Pressure is often used. If there is a leak, clean air will be ejected rather than unfiltered air entering the cleanroom.
Negative Pressure Airflow
Air is filtered out inside a cleanroom with negative pressure, resulting in lower air pressure than outside. Every window, door, and other opening is completely sealed. As a result, the Pressure in the area lowers, allowing outside air to enter the cleanroom. Negative Pressure is the top priority when stopping contamination from leaving the cleanroom.
Criteria for Selecting a Medical Injection Moulding Cleanroom Environment

- Examine the cleanroom class criteria for the project:
Class 8 cleanrooms are prevalent in injection molding factories, but if consumers prefer to make implantable medical devices, they must do so in a Class 8 cleanroom. As a result, cleanroom class requirements must match the consumer’s project specifications.
- Check to see the product that can be manufactured, assembled, and packaged in a cleanroom:
To ensure that the plastic component is as clean as possible, pick a manufacturing partner who can not only mold but also assemble and package their product in a cleanroom. This ensures that the plastic component is clean.
- Check to see if they can manufacture intricate plastic parts:
The cleanroom capabilities of an injection molding company can vary, but if the project requires the manufacture of complex plastic parts with difficult tolerances, the consumer must ensure that the injection molding company is capable of maintaining tight tolerances. This understanding is essential to ensure that each plastic component is not only clean but also of high quality.
Plastic Materials Used in Clean Room Injection Molding
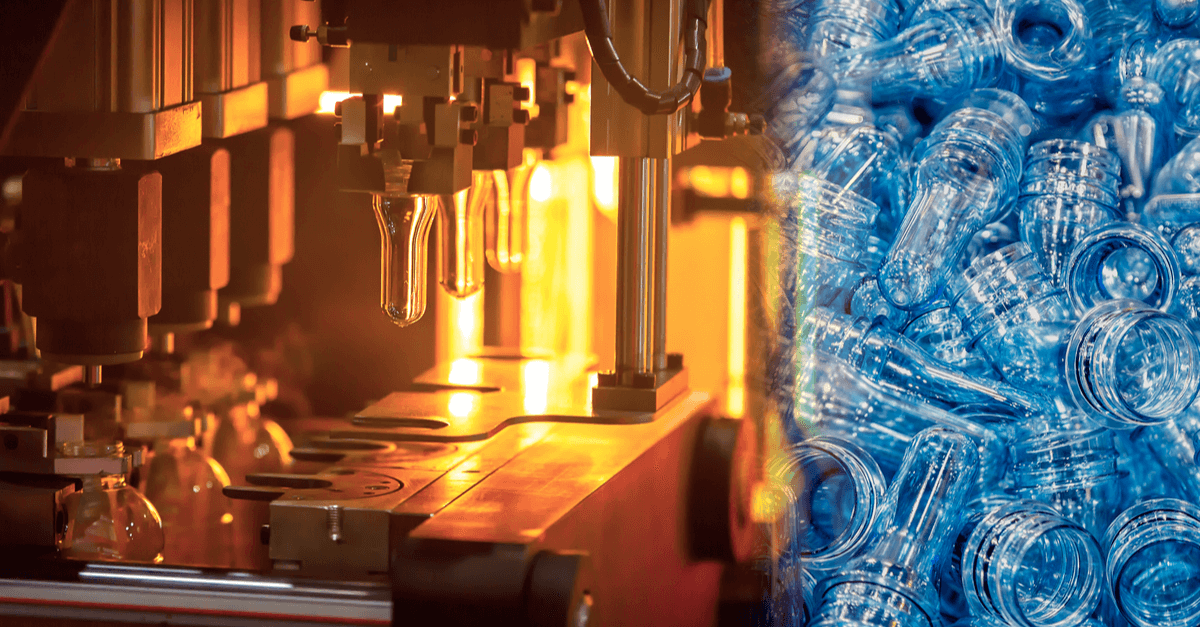
Polyethylene terephthalate
Polyethylene terephthalate (PET) is one of the most extensively used polymeric materials in the health care business. This is due to its biocompatibility, high homogeneity, mechanical strength, and resistance to chemicals and/or abrasion.
While bacterial adherence is dependent on surface properties. Such as surface charge and energy, hydrophilicity, and surface roughness; antimicrobial compounds attached to the surface can have a biocidal influence by slowing bacterial growth (bacteriostatic) or killing bacteria (bacteriocidal) (bactericidal).
As a result, it is widely accepted that imbuing PET surfaces with antibacterial properties will benefit the prevention of infectious diseases. For this purpose, various modification procedures have been reported.
In clean room injection molding, PET is melted and injected into a mold to create the desired shape. After that, the plastic is cemented by cooling the mold. Injection molding is a fast and efficient way to mass-produce components from a single mold. Clean room injection molding is used in businesses that require extreme cleanliness, such as the medical field. This approach removes contaminants that could interfere with delicate processes.
High-density Polyethylene
When it comes to High-density polyethylene (HDPE), this is a versatile polymer used in a variety of industries and applications. It is also a cost-effective thermoplastic material with numerous applications in clean rooms. One of the most common applications for HDPE is injection molding in a clean room. In clean room injection molding, HDPE is used to create parts and products that are free of contaminants and pollutants. This type of molding is typically used in industries where product purity is critical, such as the medical, food, and semiconductor industries.
The properties of HDPE make it an appropriate material for clean room injection molding. Because HDPE is a nonporous polymer, it does not absorb contaminants like porous materials. HDPE is also chemically resistant, making it ideal for usage in industries where harsh cleaning agents are used. Furthermore, HDPE has a low moisture absorption rate, which inhibits mold and germ formation.
Injection molding in a clean environment is a precise technique requiring careful planning and execution. The first step in the process is to choose the best HDPE resin for the job. The resin must be compatible with the manufacturing technique as well as the end product criteria. Following the selection of the resin, the mold must be designed. The mold must be designed to meet the application and HDPE specifications.
Polypropylene
As a result of its low melting point, polypropylene can be injected molded using the same processes that are typically used for injection molding. It is a material that is not only lightweight but also long-lasting and biodegradable. Because of this, it is an excellent choice for use in producing goods in clean rooms.
Clean rooms are specialized laboratories used in the conduct of scientific and medical research. Within these labs, the materials that are employed are handled in compliance with stringent safety requirements. The operation of clean rooms at extremely high temperatures and pressures is required in various industrial processes, including the fabrication of semiconductors.
Before it can be utilized in a clean room, polypropylene has to go through a precise processing step first. To begin, the plastic must be submerged in a solvent for a considerable amount of time. This eliminates any contaminants that may have the potential to make the clean space unsanitary. After that, the plastic must be subjected to extremely high temperatures to be prepared for injection into the mold. This guarantees that the plastic melts all the way through and can be injected into the mold without difficulty.
ABS Plastic
The thermoplastic polymer known as ABS plastic is often processed using injection molding. Because it is resistant to both chemicals and impacts, it is an excellent choice for a diverse range of applications in the industrial sector. ABS plastic has a wide range of applications and is commonly seen in places such as computer keyboards and bumpers on vehicles.
Injection molding in a clean room is the process of injection molding in an environment with very few impurities. This is done to develop goods that are free of flaws and pollutants in their production. To reach this level of cleanliness, specialized equipment and procedures are utilized throughout the process.
The first step in clean room injection molding is to choose the appropriate resin. The resin must be compatible with the specified finish and meet the purity requirements. After the resin has been selected, it is dried to remove any remaining moisture.
The next step is to prepare the mold. The mold must be cleansed and sterilized to avoid contamination. The injection machine is loaded with resin once the mold has been prepared.
The injection mechanism is then sealed and cleaned with nitrogen gas. This removes oxygen from the machine, which could otherwise cause flaws in the finished product. The nitrogen also aids in keeping the molten plastic at a consistent temperature.
PVC
Polyvinyl chloride, more often known as PVC, is a form of flexible plastic with a wide range of applications. Some examples of its use include plumbing pipes and medical equipment. PVC is an excellent material for clean room injection molding not only because it is inexpensive and simple to produce but also because it is resistant to various chemicals.
Polyvinyl chloride (PVC) is produced through the polymerization of vinyl chloride monomers. The finished plastic has excellent durability, high hardness, and dimensional consistency. Because it can be molded into various shapes and sizes, it is an excellent material for use in clean room injection molding.
PVC’s resistance to acids, bases, and salts is all part of its impressive chemical arsenal. Because of this, it is an excellent choice for use in clean rooms, which require a very high level of sterility and sanitation. Due to the fact that PVC does not burn, it can be utilized when working with combustible materials like explosives.
It may be molded into incredibly detailed and intricate shapes thanks to the material’s malleability. As a consequence of this, it is an excellent choice for applications of clean room injection molding that require accurate dimensions.
PVC is an adaptable plastic that may be utilized in many different contexts due to its wide range of properties. It is resistant to a large variety of chemicals, in addition to being affordable and simple to deal with. Due to these qualities, PVC is a good material for injection molding in sterile conditions. In addition, this is available in medical plastic manufacturer.
Can Seaskymedical Keep Tight Part Tolerances While Doing Clean Room Molding?
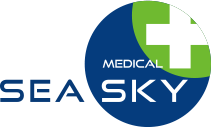
When executing clean room molding, Seaskymedical can maintain accurate tolerances. The key reasons behind this are as follows:
Seaskymedical’s cleanroom has received ISO 13485:2016 certification. The company reduces the number of airborne pollutants such as particles, toxic air, and bacteria by building clean rooms. Furthermore, the indoor environment’s temperature, humidity, pressure, air velocity and distribution, noise, vibration, illumination, and static electricity are kept within a specific range.
- Static-free
- Fewer air pollutants
- Easy-to-clean latex floors
- Proper humidity and pressure
Seaskymedical, which specializes in clean room injection molding and has a production space of 3,600 square meters, has 10 advanced plastic injection molding machines. Their medical device cleanroom is ISO 13485-2016, and CMA certified. It is considered “World Class” by our demanding partners since the genuine test results of our class 100,000 cleanroom exceed ISO 8 and are similar to ISO 7 cleanroom.
Temperature, relative humidity, and air filtration are routinely monitored to identify and eliminate sources of contamination and assure part traceability and compliance. Stringent controls validate equipment and techniques to ensure that the customer’s project is carried out with great precision and reproducibility.
A medical injection molding company must maintain a clean atmosphere when making medical products. Because all bacteria and microorganisms endanger the health of humans and animals.
As a manufacturer of medical device components, their investments in Class 7 and 8 clean rooms have resulted in enhanced efficiency and a better working environment, allowing us to offer high-quality medical items at a lower cost.
Consumers can definitely count on Seaskymedial for the following when they needs a creative and cost-effective medical plastics solution:
- Medical Disposables
- Medical Devices/Equipment Components
- Laboratory Disposables
- Medical Clean Room Assembly
- Surgical Disposable Product
- Medical Clean Room Packaging
When it comes to the organization’s handling pollutants when using their Clean room injection molding:
- Medical equipment is appropriately scaled, built, and positioned to allow for cleaning, maintenance, and operations.
- To avoid confusion and contamination, provide enough room for the appropriate installation of parts and machines.
- Control the cleanroom’s temperature and humidity.
- Install filters to keep bigger particles out of the air.
- The staff wears robes, hairnets, and overshoes.
- Sanitize the injection machines regularly.
Lastly, the company is also a medical device contract manufacturer. Contract manufacturing is a process where a medical technology business outsources Manufacturing to another medical device manufacturing firm in compliance with the OEM’s standards and following ISO:13485 and FDA criteria. Healthcare contract manufacturing is created following the OEM’s standards and requirements, guaranteeing quality and compliance with all necessary regulatory guidelines.
The company is a prominent medical device contract manufacturer with years of expertise in contract manufacturing medical equipment. The organization’s efficiency and high-quality production also help them stand out among other medical device contract manufacturing companies. Furthermore, they consider their customers’ opinions and keep them updated on the process, so they know what is happening.
Choose Right Clean Room Injection Molding Partner- Seaskymedical
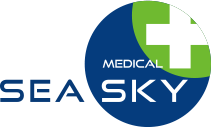
Clients looking for high-quality clean room injection molding services should work with Seaskymedical. The organization has a clean room facility that adheres to the highest industry standards, and its crew of seasoned specialists is dedicated to providing our clients with the finest possible results.
Welding, printing, assembly, packing, and clean room sterilization are among the value-added services provided by the organization. The company’s understanding of resins and medical-grade polymers enables it to create products that meet strict specifications.
In addition, the company profoundly understands materials and can work with various plastics designed for medical applications. With fourteen years of medical injection molding experience, they can also meet the medical industry’s strict criteria and tolerances due to their knowledge and abilities.
Seaskymedical has introduced micro-injection devices from Germany and Japan. The machine has a long nozzle and a modest injection capacity of 5g or 8g. The firing rate is 250mm/s, and the maximum temperature of the barrel is 450 degrees Celsius (saving glue).
Furthermore, the business provides worry-free, one-stop service from the medical item and mold design to cleanroom molding, assembly, and packaging. They provide free technical support and services for medical products and injection molding during product development to save our clients time and money.
Lastly, the company’s cutting-edge injection equipment expedites the delivery of medical injection-molded items as a dependable, clean room injection manufacturer. The company’s quickest delivery time is four weeks after a client decides to work with them and submits an order.
FAQs
What is a clean room?
Clean room molding is a type of molding used in the manufacture of medical equipment and devices. The molding is applied directly to the product to be molded and is intended to limit the growth of infectious materials. Furthermore, clean room moldings serve in the maintenance of a sanitary environment and the mobility of staff and equipment inside the space.
What are the benefits of clean room injection molding?
Injection molding in a clean environment provides several advantages, including improved product quality, reduced contamination risk, and increased efficiency.
Injection molding in a clean room environment can help to improve overall product quality by reducing the risk of contamination from dust or other particles.
Contamination risk reduced: By keeping the injection molding environment clean, consumer can help to reduce the possibility that the final product will be contaminated.
Because there is less need for effective cleaning between batches, injection molding in a clean room can also help to improve overall operational efficiency.
What are the drawbacks of clean room injection molding?
There are several potential drawbacks to clean room injection molding, including:
- High Initial Cost
Multiple design and modeling iterations are frequently required prior to approval or manufacture. After that, the injection molding tool needed to generate the molds must be created and constructed. The mold tool is a sophisticated piece of work that involves people, resources, and many hours of machining to manufacture, and it is the most expensive part of the injection molding process. Obviously, once everything is finished, the part cost is relatively low, and the repeatability for tens of thousands of mouldings is very high.
- Initial lead time
It could take months from product conception to finished component, design, testing, and tool manufacture. If consumer knows exactly what they want, however, the finished mouldings can be provided in four weeks. Moreover, once the tool is built, running the molds takes relatively little time, especially if the tool has numerous impressions.
- Large Part Size Limitations
Massive machines are required for plastic injection molding. Depending on the product, a technique such as Plastic Fabrication may be better for the manufacturing of extensive parts, which involves the use of a huge mold tool and is expensive.
- Careful design needs
Undercuts which drastically increase tooling costs, locked-in features, and insufficient draft. The material and temperature must be considered when designing the walls, or else the mold may not fill entirely. To get an aesthetically pleasing effect, the positioning of ejectors and cooling lines must be researched.
What are the guidelines for clean room injection molding?
There are a few key considerations while designing and constructing clean room injection molded parts. Clean room injection molding tools and work areas must be created and configured to restrict the amount of airborne particles. The molding technique must be adjusted to generate low levels of particle matter. All tools must be stored in a clean, cool environment, and newly purchased instruments must be put through their paces to avoid improper torque or tool usage problems.
What are the best practices for clean room injection molding?
Clean room injection molding (CRIM) is a method of producing things in a clean room. General cleaning, paint removal, interior scrubbing, and operability testing are the four basic cleaning processes used by CRIM.
General cleaning necessitates the disassembly and reassembly of all components that must be cleaned. This can be done with a professional cleaning solution or common household wipes.
Paint removal entails removing any colors or adhesives placed on the molds. This step must be followed before using a mold designed to be reusable.
Cleaning all surfaces within a clean room is what interior scrubbing includes. This can be achieved with either a professional solution or a water-and-soap mixture.
The final phase of CRIM is testing a product’s operability, ensuring that all parts fit well and that the product can be easily made. Inspecting the molds, production processes, and tools can help with this.
ISO 14644 Standard Factory for Medical Device Injection Molding
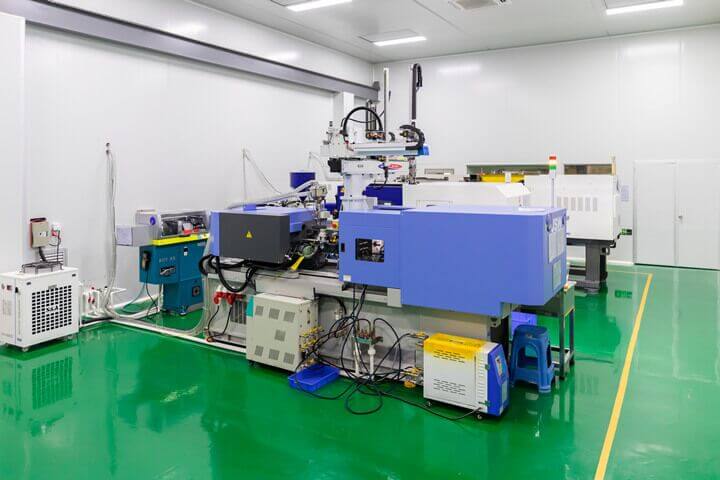
The level of air cleanliness is measured according to the ISO 14644-1 standard. ISO specifies a process and technology for medical device injection molding that ensures product quality and safety. This is determined by the usage of limit values. In addition, The ISO 14644 Standard covers the rules and regulations required to manufacture medical devices. This standard establishes a secure and stable infrastructure for medical device manufacturers who strive to develop high-quality products.
The particle concentration per cubic meter is the determining factor in the ISO classification. The purest level is ISO 1, the least pure level is ISO 9; the highest purity class is ISO 1. This cleanroom class standard is typically implemented in cleanroom systems utilized in the production of semiconductors.
Injection molds for medical devices are covered by this ISO standard for design, manufacture, and testing. Manufacturers of medical devices must adhere to a well outlined process to maintain a high level of quality and safety in their products. This standard creates an all-encompassing structure for designing, developing, and producing injection molds used for medical devices.
Conclusion
Moldings are substantial since they represent the first step in cleaning a room. Material usage is critical since it influences the overall cleanliness of the place. Furthermore, one of the key reasons they are used is to assure the comfort of the residents of the space. When deciding how to clean a room, there are various aspects to consider, such as the type of cleaning product to use, the number of times to use it, and other measures.
Those who are interested in beginning a medical-related business may find that collaborating with Seaskymedical is a good choice. With the assistance of the company’s professionals, entrepreneurs will have a much easier time getting their businesses off the ground.
Any company, regardless of its years or level of experience, stands to gain from the expertise and knowledge that the organization possesses in the medical industry. Do you intend to start your business now in the medical field? Always remember to collaborate with Seaskymedical. Contact them now, and they will be more than glad to provide for any needs