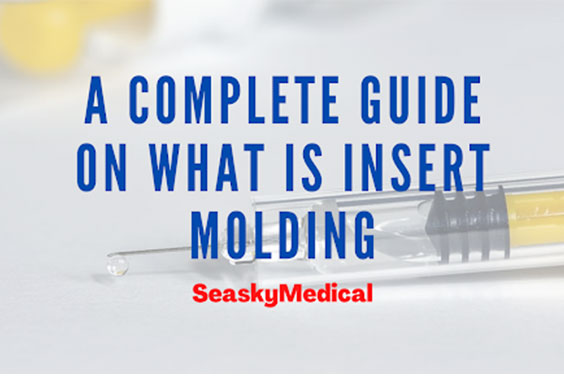
This article will provide a comprehensive overview of what insert molding is, how it works, its benefits, and how to set it up for your business. With insert molding, you can create custom products quickly and easily.
This technology lcreats plastic parts with complex shapes that are impossible with other manufacturing methods. Insert molding is perfect for products that need high accuracy and repeatability, such as medical devices or toys.
This article will look at the exact meaning of insert molding and its use.
What is Insert Molding?
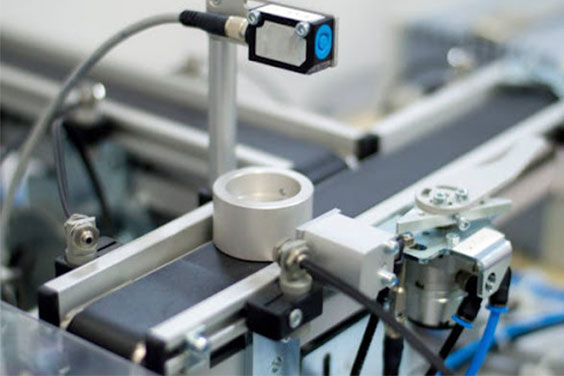
Insert molding is an injection molding similar to overmolding but not identical. Insert molding involves placing a finished component (usually metal) into a mold before injecting plastic. It allows product teams to construct ergonomic devices, power tool grips, and rubber gaskets directly onto existing components, reducing human work.
Designers and engineers can use injection molding inserts to make essential hand tools like scissors and screwdrivers or wrap metal electrical components in safe plastic housings.
For encapsulating metal components in plastic items, insert injection molding is better. Manufacturers in the automotive, medical, electrical, consumer goods, cosmetics, and other industries increasingly use insert molding technology. Product teams must overcome design and production issues to profit from insert molding.
How Does Insert Molding Work?
Molten resin is injected into a plastic mold that has been custom-made to fit the part’s geometric parameters. Plastic resins are injected and allowed to solidify in the mold. They are then ejected from the insert mold.
The primary distinction is that the metal is inserted into the molten resin before closing the mold. The plastic entirely encases the product, and the entire core product is swallowed up by the plastic, with no visible cracks and a uniform wall thickness.
The inserted object can be as straightforward as a blade or a tube or as intricate as a metal insert for a sophisticated machine. Insert molding is popular because it eliminates the need to screw together multiple plastic parts to create a product cover.
The product is contained within the covering, which naturally forms around it due to the mechanical bond. CNC machining provides a pleasant grip and a product design of excellent quality.
The Insert Molding Process
Insert molding is distinct from regular injection molding. Specific components are put in the mold before the molding material is applied. It is analogous to the overmolding technique. These additions are available due to the mold’s design. Keep the inserts in their respective locations to retain their place and orientation during the material injection. These components can be introduced manually or automatically into the mold. This is a simplified version of the procedure:
Step 1: The component is secured inside the mold using a retainer.
Step 2: Pour molding material into the mold and allow it to flow around the insert.
Step 3: While the product is still encasing the insert, remove it from the mold.
What are the types of insert molding?
- Metal Insert Molding
This is a mechanical technique for enclosing metal inserts in plastic. This kind of molding is frequently employed in the production of plastic molded products. Metal inserts must be positioned precisely to ensure proper part geometry.
- Plastic Insert Molding
Plastic is a versatile material utilized to create a wide array of items. Medical plastic injection molding is a process that allows for the incorporation of small plastic components into larger plastic objects, such as the front cowl on the hull of a boat.
- Glass Insert Molding
When glass inserts are used in plastic molds, this is what happens. Glass injection molding is not the same as injection molding. Glass produced by this method is frequently smaller in size than glass produced by injection molding. Glass is used to provide transparency in parts of a product and to aid in the creation of specific shapes and designs.
- Silicone Insert Molding
Silicone is used as the molding material in this form of insert molding. Silicone insert molding is accomplished by combining the flowable silicone resin with the basic resin. Following that, the silicone mixture is injected into the mold together with the other components. The silicone solidifies after a few heating and cooling cycles, and the pieces are taken from the mold.
- Cavity Insert Injection Molding
The cavity is constructed by two movable single part injection molding cavity halves in this type of insert molding. A hinge links the two mold components and serves as a connector.
- Insert Compression Molding
Typically, it is used to make custom plastic parts. Compression molding involves injecting plastic into a mold and then compressing to remove the surplus resin. After opening the mold, the piece is ready to be released.
- Film Insert Molding
Film Insert Molding is a method similar to insert molding. However, a thin film of plastic is applied around the product during this operation, effectively overmolding it. It is done to prevent contact between the metal insert and the product.
What Materials Are Commonly Used in Injection Molding?
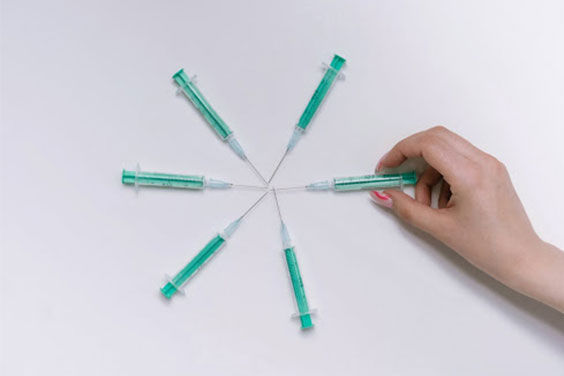
Depending on the requirements, such as cost and product shape, injection molding can be used with plastics. The following are the most frequently used plastic materials:
- Acetal
Acetal, also known as Dupont Delrin, is a durable and long-lasting plastic used in various applications. It is a type of technical plastic widely used in injection molding. SYRINGES and surgical guides are just two examples of medical insert molding devices that contain this material.
- Acrylic
It is a transparent thermoplastic that is often used to produce injection molds. It is used in the manufacture of ornaments, decanters, and closures. Acrylic exhibits a degree of clarity that glass, another of its primary competitors, struggles to match. Use acrylic to create caps, closures, and crowns. Use acrylic to fabricate components and fittings for various instruments and measuring equipment, including pH meters and optical devices.
- Acetal Copolymer
The plastic used in injection molding. This thermoplastic polymer is also referred to as Dupont Delrin. Chemically, it is comparable to POM and PP. It’s used to make small parts and gears. It’s a rigid, hard plastic. Low-maintenance, no-polish objects result.
- ABS
It is a form of impact-resistant plastic that is particularly well-suited for applications that require a high level of durability. The material can be any color, including black, white, red, and other hues. Transparent ABS molding is used in the majority of ABS parts. It protects a range of products, including electrical connectors, toys, and other medical consumables like luer connector.
- ASA
It is the most often utilized polymer in the manufacture of medical devices. The three primary qualities of ASA are its resistance to heat, durability, and high machining quality. ASA is a versatile substance utilized in various applications, including medical equipment, dental supplies, and dental implants.
- Delrin
Delrin is a low-cost acetal-based thermoplastic. It is lightweight, may be strengthened, and is utilized in various applications, including outdoor and medical equipment. Additionally, it is affordable and used to create many identical parts. Due to its inability to endure high temperatures, this plastic is not used to manufacture low-temperature goods.
- POM
POM is an abbreviation for polyoxymethylene, often referred to as acetal resin in some areas due to its similarity. In addition to gears, bearings, valve seats, insulators, and car trims, this easy-to-form polymer is used in various other applications.
- PEEK
With its excellent heat resistance and mechanical stress, it is commonly used as a mold material in producing plastic molds. In addition, it is a substance that adheres well to the metal insert.
Insert Molding Materials
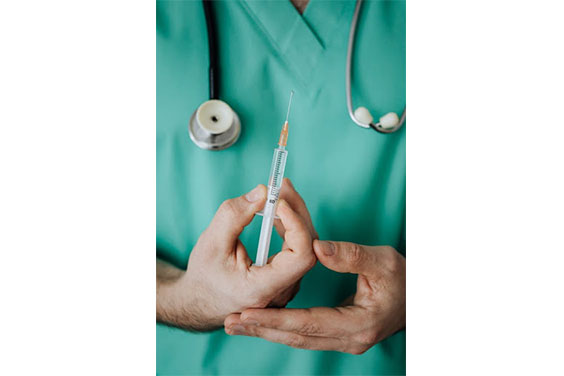
Insert molding techniques employ a range of materials. The molding substance or plastic resin is selected based on the mold, the product’s material, and other factors such as chemical bonding, additive manufacturing, mechanical bonding, and the finished 3D print product’s wall thickness. The primary objective is to maintain the mold’s viability and durability during the molding process.
- Thermoplastics
Thermoplastics are environmentally friendly materials utilized in the plastic molding process since they may be reused several times. Thermoplastics are chemically resistant and are an excellent choice for assuring uniformity and gloss throughout the molding process.
The following are the most frequently used thermoplastic materials on the market:
Polyethylene
Chemical resistance, hardness, dielectric qualities, and impermeability are all characteristics of this thermoplastic polymer. The most prevalent polyethylene thermoplastics on the market are HDPE, MDPE, and LDPE. They are made of thermoplastic materials that are incredibly lightweight.
Polystyrene
These polymers are transparent, flexible, and have a low melting point. They are acid and basic resistant and are found in various everyday products, including consumer goods and medical devices.
Nylon
Nylon is a long-lasting substance that is chemically and abrasion-resistant. Its high melting point uses it in some applications in place of metal. So Nylon injection molding is a popular material for heavy-duty applications such as manufacturing and extraction.
- Thermosets
Thermosets, like thermoplastics, cannot be recycled and are therefore not very eco-friendly. The following are some examples of thermosets that can be used to make stainless steel medical equipment.
Phenolic
Typically, the material is certified to IL 94V 0 and has a high chemical resistance to halogenated solvents. When specific constraints exist, they are applied to highly specialized operations.
Epoxy
They become permanently hardened and have no melting point following processing. As a result, they are well-suited for high-performance applications. They exhibit superior resistance to heat and chemicals and excellent adhesion.
- Elastomers
Elastomers include rubber and various synthetic and natural polymers. These polymers are significant due to their flexibility and recyclable nature. They are exceptionally environmentally friendly materials well-suited for household appliances and car manufacture.
Liquid Rubber Silicone
It is a material utilized for its high abrasion resistance and heat resistance. It is a flexible, lightweight, and rubbery substance used for products with complex geometries.
Natural Rubber
Natural rubber is incredibly durable and flexible. It is used to make tires and a range of other household items.
Polyurethane
Polyurethane is abrasion resistant and has a strong resistance to wear and tear. This material is both elastomeric and resistant to impact. The material is tough and resistant to heat.
- Glass
An excellent example of a material that is used in insert molding. It’s an incredible substance. Its thermal expansion and viscosity are high. The material is heat resistant.
It is also non-corrosive. Glass acts as a barrier between metal and plastic. And Glass is also utilized to make metal items. Glass is impervious to metal. Hence metal and plastic cannot mix.
Advantages of Insert Molding

Insert molding offers a number of advantages. Perhaps you’ve noticed a few of them here:
Costs of Production
If you employ typical injection molding, you’ll need to add a second manufacturing process to join different-material inserts. In comparison, the insert molding process combines the molding and secondary manufacturing phases into a single super step, resulting in cost savings associated with more people, factory space, and managerial capacity.
Quality Assurance
When insert molding is performed in a highly automated manner, the requirement for a robust quality control plan is significantly reduced. Due to the limited number of manufacturing steps, systematic and human errors are significantly reduced.
Due to the extraordinary precision of the equipment, any spatial imperfections can be eliminated through the use of industrial robots in a well-designed molding process.
Optimal Material Utilization
It is possible to optimize the influence of material attributes by integrating two or more materials into a single final product. For instance, a plastic gear assembly may only require the mechanical qualities of steel in its middle.
Insert molding enables the maker to employ the most expensive materials only in the most critical areas, saving money and weight in other areas.
Structural Integrity
In comparison to standard molding, machining, and assembly, insert molding produces a material marriage that is substantially better. Due to the creative use of undercuts and shoulders, a threaded brass insert, for example, may withstand torque and tensile force much better.
Traditional methods, such as heat staking and ultrasonic inserting, which are utilized for samples and prototypes or extremely low volume manufacturing, do not allow for complete integration of the insert into the parent material.
Aesthetics
Insert molding using plastics can result in an aesthetically pleasing finish. This is illustrated by comparing an insert molded product to one that is built of structural steel.
As a result, a well-designed insert molded product can function as a structural component in concealed areas while simultaneously delivering a high-quality plastic finish in visible areas.
Disadvantages of Insert Molding
There are also disadvantages that you’ll need to consider, and here are the following:
Sharp Corners and Undercuts
Extensive use of undercuts and sharp corners requires a mold to be designed carefully. The mold can become blocked, which can then lead to under-injection or injection leaks, or worse, damage or destruction of the mold.
Tooling
Insert molding does not offer the same flexibility as injection molding when designing and changing the tooling. Though it is possible to insert various parts, the tooling is often custom-designed for specific insert molding applications. It can be challenging to design and build insert molding tools.
Material Choice
The inserts must be used with compatible materials. If you use plastic with specific properties, you’re stuck with it. You cannot change the material. Interchangeability
Insert molding creates particular parts. There is no interchangeable quality.
Quality and Consistency
Inserts need to be precisely located in the mold. This is difficult to accomplish manually and even more challenging to automate. The manufacturing difficulties are increased when multiple inserts are used. As a result, it is difficult to attain the highest level of quality consistency.
However, if a product requires long manufacturing runs, this disadvantage can be lessened by implementing a design that can be fully automated.
Applications of Insert Molding
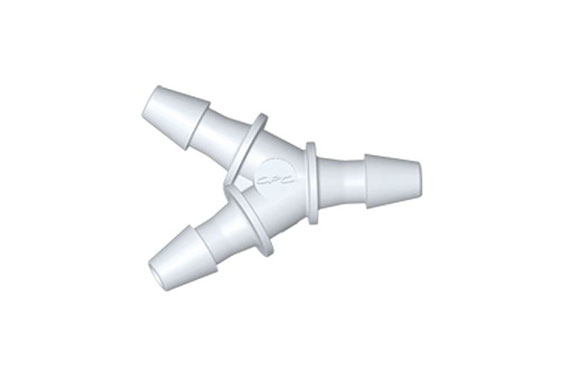
Insert molding is cutting-edge technology in plastic injection molding, as previously stated. Additionally, it is thought to be more efficient than more traditional procedures.
Insert molding is famous for its cheaper assembly and labor costs, but it also enhances component functioning by lowering part weight and size while boosting part strength and structure.
This is probably why insert molding is utilized in various industries, including automotive, consumer items, medical, electronics, and aerospace.
Insert molding is in high demand for various applications, from medical insert molding and medical plastic injection molding equipment such as tube valves and needle hubs to knobs for electrical appliances, switches, electrical components, and assemblies.
Insert molding technology is also used to create compact objects since it is completed on significantly smaller machinery. As a result, the final product is relatively compact. Overmolding produces many more essential items at a high cost in terms of time.
Injection molding is ideal for tiny commercial products that require a soft grip, additive manufacturing, or laser sintering.
Overmolding is frequently used to build components for large machinery since this method of mold tooling results in a solid and lasting product.
Insert molding also offers a long-lasting, high-quality product, but not on an industrial scale, as it requires a unique design to be manufactured.
While plastic insert molding can be done at home or in small garages, overmolding requires a dedicated production location for product development and design engineering, such as a plastics manufacturing firm.
What Factors Need to Consider When Insert Molding?
There are several factors that product development teams need to consider when inserting molding. Once the idea is turned into a design, product teams must select the perfect design and molding process. This involves considering several factors, such as:
- Mold Tooling
It is the costliest consideration. Tooling is required to ensure the insert is in the proper location throughout the injection process.
- Stress-strain for the specific material
It is a vital parameter for the success of insert molding. The insertion process must occur at the optimum temperature when the resin is in its most dense state.
- Preheat Before Molding
It is essential because it helps the resin run smoothly through the mold. The final product will come out with a more excellent finish. A preheating time of around twenty minutes is required when the resin temperature is over 180 degrees Celsius. Approximately forty minutes are necessary when the temperature is between 120 and 180 degrees Celsius.
- Adding Draft Angles
Is a common way to remove any burrs or sharp edges from the part. It is done by adding a few degrees to the walls of the mold tool. This decreases the chance that they will be injured while removing the part from the mold and reduces tool wear.
- Undercuts
Is when there is an incomplete molding of a nearby area. Undercuts are one of the most significant issues facing product development teams. To fix this issue, the talented engineers at the mold shop will often use the design to create supporting structures, which may be made of brass. These structures then have secondary cavities, which accept inserts. These inserts are placed in the mold before the injection molding process.
- Wall Thickness
This is needed because the pressure exerted by the clamping force of the closed mold will cause the insert to flow outward. Changes in wall thickness can impact the product design and its functionality.
- Insert Injection Molding Machine
This is the factor needed to consider because it is what will make the process possible. The machine will produce the finished product you will be proud of. You can choose from many types of machines to produce your finished product and the price at which you will be able to purchase the machine.
Overmolding vs. Insert Molding
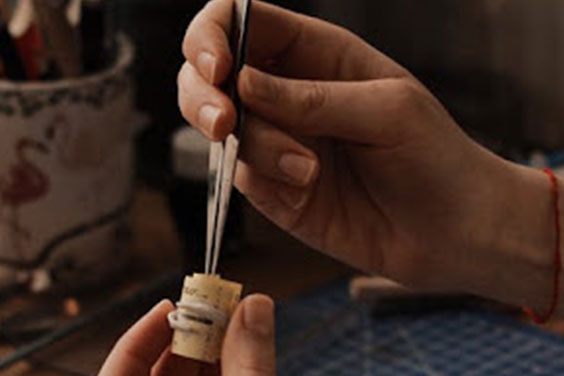
While overmolding is used to eliminate assembly costs, insert molding is used to eliminate manufacturing costs. The latter is a widely-used process in several industries. Overmolding is anywhere from 20-50% faster than insert molding, though insert molding still has its advantages.
Overmolding is a process that combines and simultaneously bonds two components, while insert molding is a process that combines and simultaneously bonds a finished element to a substrate. Overmolding is significantly faster than insert molding. The one disadvantage of overmolding is that the sonically-welded bond can eventually fail due to thermal stress.
If you are looking to combine different materials without the need to use screws to keep them together, both over-molding and insert molding can be good choices. Overmolding makes the surface more attractive and easy to clean, while insert molding makes the surface more ergonomic and easy to grip.
What Insert Molding Services Seaskymedical Can Offer?
Seasky Medical serves you with medical injection molding solutions from design to tooling to material selection and manufacturing. Contact their specialized team and help your business grow. These are the services that they offer:
- Evaluate the Optimal Manufacturing Strategy
They are known for their product design and development, including new mold design and mold making, manufacture of pre-production prototypes for testing and evaluation, the start of production tooling, and product launch. SeaskyMedical can help reduce your development cycles and improve product quality.
- Product Development
SeaskyMedical makes precise molds as well as medical plastic products. As a first step, they research DFM. Importance of strategy and execution in injection molding. The company applies the best design for your product with the best materials and manufacturing process. So, contact them early in the product development process.
- Injection Mold Material Selection Guide
Additionally, they assist with the injection molding process. The injection molding material can affect component performance parameters such as part strength, fatigue resistance, thermal properties, and chemical resistance. SeaskyMedical will make material recommendations for your project.
- Free Insert Mold Tooling Design and Manufacturing
The streamlining process is accelerated by the precise design of injection molding tools. It also reduces costs, improves daily operations, and has an impact on product quality. Seaskymedical offers FREE mold tool design services as well as injection molding alternatives that utilize cutting-edge technology.
- DFM and Flow Analysis Simulations
They also offer Design For Manufacturing (DFM) and flow analysis simulations and perform a Manufacturing Readiness Review (MRR) based on the customer’s final design.SeaskyMedical helps customers increase production cycles and obtain high volumes by providing design for manufacturing (DFM) and flow analysis simulations.
- 3D Rapid Prototyping
Precision molding tools are designed using cutting-edge technology such as SolidWorks, AutoCAD, Master CAM, and Mold Flow MPI. We’ll develop a prototype using the mold design as a guide. 3D printing enables rapid development prior to finalizing the client-supplied mold design for mass manufacturing.
- CNC Plastic Machining
CNC machining employs high-speed cutting tools to design metals and plastics. Steel, magnesium, titanium, and even highly engineered polymers and carbon fiber can be machined with CNC plastic machining. For manufacturers, this means many manufacturing processes.
- Full-scale Contract Manufacturing
Seasky Medical is a seasoned contract maker of medical products. Their process efficiency and high-quality production set them apart from other medical device contract manufacturers. They keep their clients updated on the project’s progress and invite their feedback.
- Parts Assembly and Packaging
They give complete packaging solutions by delivering medical assembly and packaging services. They can provide assembly services, packaging supplies, machinery, and assembly facilities, among other things.
- Pad Printing & Uv Welding
This is the most often used system of labeling. Seasky Medical uses UV welding and laser welding to combine plastic and glass containers. Additionally, this technique can be utilized for pad printing and labeling.
Insert Molding Design Guide
The insert molding design guideline benefits the manufacturing process in a variety of ways. Insert molding design criteria are comparable to those for conventionally molded goods. Frequently utilized guidelines include maintaining consistent wall thickness, introducing draft for part ejection, and so forth.
- Insert Molding Design
Insert molding techniques employ a range of materials. The molding substance or plastic resin is selected based on the mold, the product’s material, and other factors such as chemical bonding, additive manufacturing, mechanical bonding, and the finished 3D print product’s wall thickness. The primary objective is to maintain the mold’s viability and durability during the molding process.
- Product Design
Product design benefits the insert molding process in a variety of ways. Design criteria are comparable to those for conventionally molded goods. Industrial designers and engineers will want to consider the molding process as part of the product’s design. Frequently utilized design considerations include part strength, part assembly, part appearance and aesthetics, and safety.
- The Machinery
For product development, the approach demands the use of advanced molding equipment. Vertical machines are used in the plastic molding process for insert injection molding and must adhere to a set of design requirements specified by the engineering team.
The machines have an exceptionally tight tolerance, which ensures the precision of the plastic arts information used in plastic injection molding. A slight millimeter misalignment might result in the failure of a product.
- Threaded Inserts for Injection Molding
IT is a process that involves the insertion of a metal or metal alloy component into a plastic component. This is performed by threading the metal component to match the diameter of the hole in the plastic part, which has been lathed to a certain tolerance.
After inserting the metal component into the hole, it is either cemented or epoxied in place. Threaded inserts are a type of fastener assembly distinct from conventional fastener assembly. They are utilized when fasteners are concealed or difficult to access following construction. There are numerous materials available for threaded inserts.
Conclusion
We believe you will be impressed by the insert molding design guidelines, machinery, and technique that we have put together to help any business grow. Keep in mind that, Insert molding is a technique for creating a finished product that is both functional and aesthetically pleasing to the eye.
Contact Seaskymedical for more information on insert molding; they provide the most excellent services for your medical insert molding needs.