One of the most widely accepted ways for producing plastic parts and components is injection moulding. Its use has become integral in many industries due to its low-cost production capabilities. It is an efficient way to generate large amounts of high quality plastic parts that are equally precise and strong.
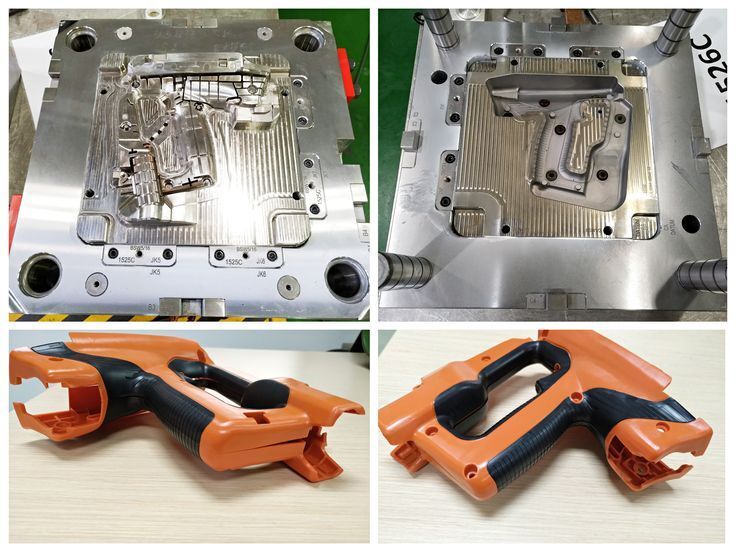
Today, one of the most popular injection moulding techniques is 2K injection moulding that involves two or more different materials being combined in the same mold before being injected into the part shape. Knowing about the 2 shot molding design guidelines is important for achieving optimal results in the molding process. Here, it will discuss everything a buyer needs to know about 2K injection molding and its uses in business.
What is 2k Moulding?
2k injection moulding is a type of plastic injection molding process that uses two shot molding design to produce a single part. It is beneficial to the manufacturing industry because it reduces costs by eliminating the need for painting and post-molding operations while still producing a high quality, consistent product.
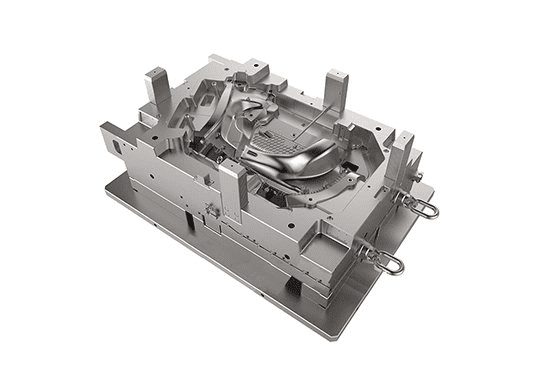
During the 2K molding process, both materials are simultaneously injected into the mold cavity. The first material is usually a rigid material like polypropylene and the second material is typically an elastomeric material such as TPE or TPV. The combination of two materials allows for more complex designs and better functionality than traditional single-material injection molding.
Common Applications of 2k Injection Moulding
2k injection molding, also known as two shot molding design injection, is highly versatile and can be used to create complex and intricate parts with various design features. The most common application of this moulding process is the medical industry.
- Syringe plungers – Two shot injection moulding is used to produce syringe plungers with a soft, flexible tip that is easy to use.
- Inhalers – It is used to create inhalers with a soft, flexible seal that fits tightly around the mouth.
- Contact lens cases – It is used to produce contact lens cases with a soft, flexible lid that prevents contamination.
- Medical tubing – It is used to produce medical tubing with a soft, flexible end that fits comfortably in the patient’s body.
- Surgical instruments – The process is used to create various surgical instruments like forceps and clamps that require precise designs and materials.
Some common applications of 2k injection molding other than the medical industry include the automotive industry, consumer electronics, household appliances packaging industry, sports equipment and toys.
How Does 2k Injection Moulding Work?
The double injection molding is a highly efficient manufacturing process that allows for the creation of complex, multi-material parts with high precision and tight tolerances. According to the two shot injection molding design guide, the process starts with the injection of the first material, usually a rigid thermoplastic, into a mold cavity to create the first shot of the part.
Once the first shot is complete, the mold rotates or moves to a second station, where a second material, often a softer or more flexible material, is injected into a specific area of the first shot.
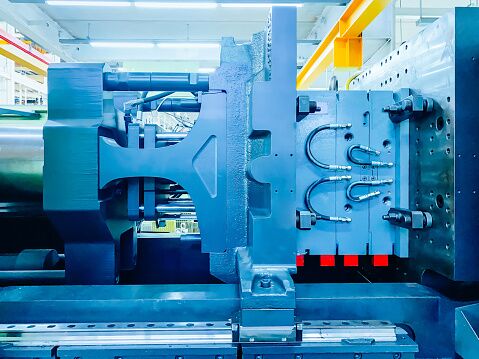
The second shot can be used to create a variety of effects, including adding a different color or texture to the part or providing additional functionality, such as soft-touch over-molding or hard, structural support. For example, a two-shot molding process can be used to create a toothbrush with a hard handle and a soft grip area, all in one molding cycle.
The 2 shot molding process is ideal for creating parts with complex geometries, such as gears or multi-component assemblies, as it allows for precise placement of the second material. Additionally, the process can help reduce production times and costs as it eliminates the need for separate molding and assembly operations.
The Benefits of Using 2k Injection Moulding
There are numerous benefits to using 2k injection molding in manufacturing. Here are some of the key advantages:
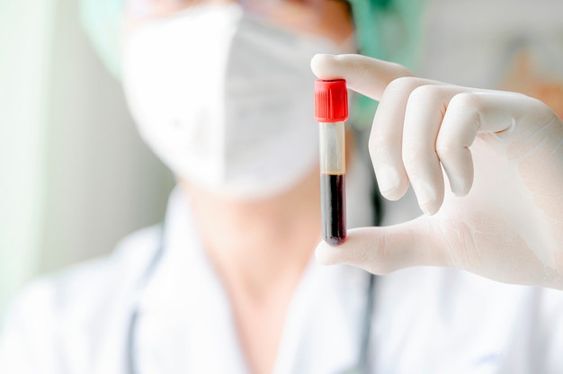
- Versatility: The two shot molding process allows for the creation of complex, multi-material parts with different colors, textures, and functional features, all in a single molding cycle. This versatility reduces the need for multiple molding and assembly operations, resulting in faster production times and reduced costs.
- High Precision: The 2k injection molding process enables manufacturers to achieve high precision and tight tolerances, making it an ideal choice for creating parts with intricate geometries, such as gears and multi-component assemblies. With this process, manufacturers can produce parts with intricate shapes and sizes that may be difficult or impossible to achieve with traditional molding methods.
- Enhanced Functionality: By incorporating multiple materials with different properties, 2k injection molding can create parts with enhanced functionality, such as soft-touch over-molding, structural support, or improved grip.
- Improved Aesthetics: The ability to incorporate multiple colors and textures in a single molding cycle enables manufacturers to create parts with a more attractive and aesthetically pleasing appearance, enhancing the value of the final product.
- Reduced Assembly Time: By combining multiple materials in a single molding cycle, the 2 shot injection molding eliminates the need for separate molding and assembly operations, reducing the overall assembly time and costs.
- Lower Waste: The double-shot injection molding process minimizes waste by allowing manufacturers to use only the required amount of material to create a part, reducing scrap and minimizing environmental impact.
The Downsides of Using 2k Injection Moulding
While double-shot moulding has several advantages, it also has some drawbacks that should be taken into account before choosing it as a manufacturing process.
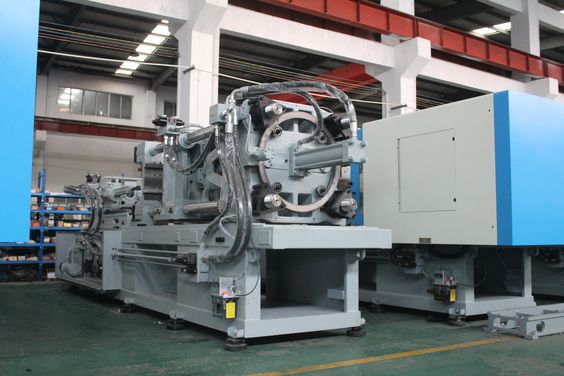
- High initial investment: The equipment required for the 2k injection molding process is more expensive than traditional injection molding equipment, which can make it more expensive to set up initially.
- Complex process: It is a more complex process than traditional injection molding, which requires specialized knowledge and experience to set up and run.
- Longer cycle times: The 2 shot molding process typically requires longer cycle times than traditional injection molding, which can affect production output and lead times.
- Limited material selection: Some material combinations may not be compatible with the double shot molding, limiting the available material options for the final product.
- Maintenance requirements: 2k injection molding equipment requires regular maintenance to keep it running efficiently and minimize downtime.
Requirements for 2k Injection Moulding
To guarantee that the final product meets the required 2 shot molding design guidelines, several requirements must be met. In addition, special requirements apply when producing medical devices using the 2k injection molding process.
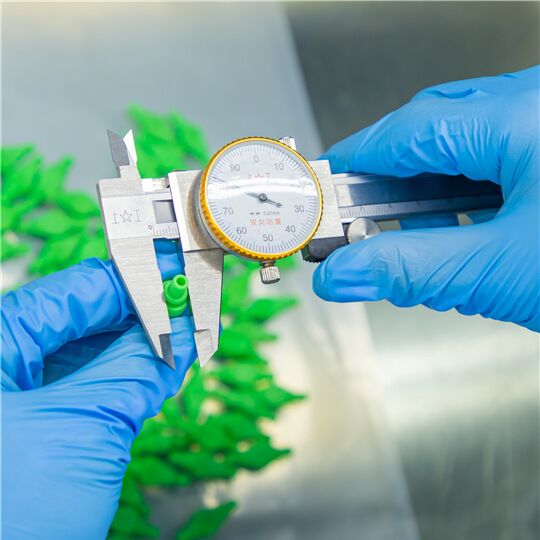
Material Requirements
In a two shot molding design guide, the selection of materials is a critical aspect of the process, as the compatibility of the materials is essential for producing a high-quality finished product. The materials used in molding must have similar melt temperatures to ensure they bond together properly. If the melt temperatures are not similar, the materials may not bond effectively, leading to poor adhesion and a weak bond between the two materials.
The hardness of the materials is also an important consideration in the twin-shot injection moulding process. Typically, the harder material is injected first, as it is more difficult to inject a softer material over a harder one. This sequence of injection ensures that the softer material can flow and fill any gaps or voids that may exist in the harder material, resulting in a more complete bond between the two materials.
The choice of materials used in 2 shot mold should be based on the final product’s intended use and performance requirements. For example, if the final product is intended for use in a harsh environment, the materials chosen should be able to withstand extreme temperatures and exposure to chemicals. Conversely, if the final product is intended for use in a consumer product, the materials chosen should be safe and non-toxic.
Process Requirements
The 2k injection molding process requires specialized equipment and trained operators who are skilled in operating the equipment and understanding the process. The equipment used in 2k injection moulding includes specialized machines that have two injection units, each capable of injecting a different material. These machines also have a rotating or sliding mold, which allows the two materials to be injected into the same part at different stages.
To ensure the success of the multi color injection molding, it must be carefully controlled to ensure that the two materials are injected in the correct order and that the bonding process occurs correctly. The injection speed and pressure, as well as the timing of the injection, must be carefully monitored to ensure that the two materials are injected in the correct sequence and at the appropriate time.
Additionally, the process must be optimized to ensure that the materials bond together properly, resulting in a strong and durable finished product.
Temperature control is another critical aspect of the 2k injection molding process. Both materials must be melted at the same temperature to ensure proper bonding, and the temperature must be carefully monitored and controlled throughout the process to ensure that the materials do not overheat or cool too quickly.
Mould Requirements
The mold used is a critical component of the process and must be carefully designed to ensure that the two materials are injected correctly and that the finished product meets the desired specifications. The 2 shot mold must be designed with two separate cavities to hold each material, and these cavities must be designed to prevent any material leakage between them.
Based on the two shot injection molding design guide, the mold must also be designed with an indexing system that ensures the two cavities are correctly aligned. The indexing system is typically a mechanical or hydraulic system that rotates or slides the mold to position the second cavity accurately, allowing the second material to be injected precisely into the correct area of the first shot.
The mold used in custom plastic injection molding must also be designed to minimize any material leakage between the two cavities. Any leakage can result in the two materials mixing prematurely, leading to poor bonding and a defective finished product. To prevent this, the mold must be designed with a seal that separates the two cavities and prevents any material from leaking between them.
Additionally, the mold must be designed with sufficient cooling channels to ensure that the materials cool and solidify correctly during the molding process. Proper cooling is essential to ensure that the materials bond together effectively and that the finished product meets the desired specifications.
The mold must also be designed to accommodate any additional requirements for the final product, such as over-molding or inserts. The mold must be designed to accommodate these additional requirements and ensure that they are incorporated seamlessly into the final product.
The mold used in double injection moulding is a critical component of the process and must be carefully designed to ensure that the two materials are injected correctly and that the finished product meets the desired specifications. The mold must be designed with two separate cavities, an indexing system, and a seal to prevent material leakage between the two cavities.
Design Guidelines
Designing a product for double shot injection molding requires careful consideration of the unique properties of the two materials used in the process. The design must be optimized to ensure that both materials bond correctly and that the final product meets the desired specifications. Here are some design guidelines to be considered:
- Material Compatibility: The materials used in 2 shot molding must be compatible with each other to ensure proper bonding. The two materials should have similar melt temperatures to ensure that they melt and bond together correctly. The materials should also have similar hardness to prevent any stress points or areas of weakness.
- Part Design: The design of the part, such as medical injection molding parts, must be produced using 2k injection molding and must take into account the specific properties of the two materials used. The part must be designed to ensure that both materials bond correctly and that there are no areas of weakness. The part should also be designed to minimize stress points and ensure that it can withstand any intended use or load.
- Gate Location: The location of the gate, or the point where the materials enter the mold, is critical to the success of the two shot injection molding process. The gate location should be carefully chosen to ensure that both materials are injected correctly and that they bond together effectively.
- Wall Thickness: The thickness of the part’s walls is also an important consideration in 2k injection molding. The walls should be designed to be as uniform as possible to prevent any areas of weakness or stress points. Additionally, the wall thickness should be designed to ensure that the part can withstand any intended use or load.
- Draft Angles: The design of the part should include draft angles to ensure that the part can be easily removed from the mold. The draft angles should be designed to ensure that there is no damage to the part during the ejection process.
By following these design guidelines, it is possible to produce high-quality parts using 2k injection molding. The design of the product must take into account the unique properties of the two materials used and be optimized to ensure proper bonding and strength.
Special Requirements for Medical Applications
When producing medical devices using 2k injection molding, there is a special two shot molding design guide that must be met. One of the most important considerations is ensuring that the materials used are biocompatible, meaning that they do not have any harmful effects on living tissue.
This is especially critical for medical devices that will be implanted in the body or come into interaction with bodily fluids, such as syringes or catheters. In addition to biocompatibility, the manufacturing process must be carefully controlled to prevent any contamination of the final product. This includes ensuring that the equipment used in the process is properly sterilized, and that all materials and components are thoroughly tested for purity.
Having a clean room injection moulding facility is needed when producing medical devices to ensure that they are safe and effective for use in a medical setting. In some cases, medical devices produced using 2 shot injection molding may also be subject to additional regulatory requirements.
For example, in the United States, medical devices are mandated by the Food and Drug Administration (FDA), and must meet certain standards for safety and effectiveness before they can be marketed and sold.
How To Choose the Best 2K Injection Molding Service?
Choosing the best 2K injection molding service is not an easy task but there are certain things to look for when selecting a provider. First and foremost, buyers should ensure the injection molding companies are ISO certified. This means that they have met all of the necessary health and safety regulations while also producing quality products to the exacting standards expected by companies worldwide.

When choosing an injection molding company, it’s important to research what services they offer, such as design and manufacturing capabilities, rapid prototyping, machinery maintenance, and post-production services. Make sure the company can fulfill your requirements before signing a contract.
Seaskymedical, is one of the reputable automotive injection companies based in China. We are a well-known provider of superior quality 2K injection molding services with more than 15 years of experience in this field. Seaskymedical specializes in medical injection molding and offers low-risk solutions.
We offer comprehensive and professional support at all stages of the project, including product development, mold design and manufacturing, material selection, and injection molding production. We used high-quality raw materials supplied by the most credible companies. These materials range from Rubber, Thermoplastics, Nylon, Thermosets, Acrylonitrile styrene acrylate, Polyvinyl chloride, Polycarbonate, Fibre-reinforced plastic, and many more.
Precision and high tolerance 2-shot injection moulding process machines are used at Seaskymedical, and we will be upgraded every three to five years. We have advanced measuring instruments, as well as high-end CNC machines and EDM machines.
Furthermore, Seaskymedical uses sterile raw lights and advanced machines to produce high-quality, low-cost two-shot molding products. Even large quantities of 2 shot mold products can be purchased at a reasonable price.
Frequently Asked Questions
2k injection molding offers several advantages over traditional injection molding, including reduced material waste and improved product performance. But some still do not understand what this type of process is and its benefits. Here are some frequently asked questions about 2k injection molding.
What are 2K and 3K Molding?
2K molding—also known as two-shot or two-component molding—injects two materials into a mold to form a part. After the mold turns or goes to a second station, another material is injected into a specific area of the first shot.
3K molding, also called three-shot or multi-component injection molding, is similar to 2K molding but uses three components to form a part. Two injection units fill a mold with diverse materials. After injecting and bonding the first two materials, the mold goes to a third station to inject a third material into a part area.
What is 1K Injection Moulding?
1K injection molding, also known as single-shot molding, is a traditional injection molding process that involves the injection of a single material into a mold cavity to create a finished part. This process uses one injection unit and one material hopper, which holds the raw plastic material in pellet form.
The material is melted, injected into the mold, and allowed to cool and solidify before being ejected from the mold. 1K injection molding is a widely used manufacturing process in various industries, including automotive, medical, and consumer goods.
What is the Difference Between 2K and Overmolding?
Both 2K injection molding and overmolding are multi-shot injection molding processes used to produce parts with multiple materials or colors. There are, however, several significant differences between the two processes.
2K injection molding involves injecting two different materials into a mold cavity in a specific sequence to create a single, two-material part. The materials are typically different colors or have different properties to achieve a specific function, such as a hard outer shell with a soft-touch inner surface.
Overmolding, on the other hand, involves molding a second material over a pre-existing part or substrate to create a part with a functional or aesthetic improvement. The overmold material typically bonds with the substrate to create a single, cohesive part. Overmolding is commonly used to add grip, improve ergonomics, or provide a soft-touch surface to a part.
Another key difference between 2K injection molding and overmolding is the complexity of the process. 2K injection molding requires specialized equipment and trained operators to ensure that the two materials are injected in the correct order and that the bonding process occurs correctly. Overmolding, on the other hand, typically requires less complex equipment and can be performed using standard injection molding machines.
2K injection molding and overmolding have distinct design requirements. 2K injection molding needs careful consideration of material compatibility, hardness, and product use and performance. Overmolding requires careful evaluation of the substrate material’s ability to bond with the overmold material and the part’s desired appearance and function.
Final Thoughts
2K injection moulding is a versatile process that offers several advantages over traditional injection moulding. It can be used to create complex and intricate parts with various design features in a wide range of industries like medical industries.
Though it requires specialized equipment and involves higher upfront costs and longer cycle times, 2K injection moulding provides numerous benefits such as reduced material waste, improved product performance, and more efficient production.
Seaskymedical is one of the popular manufacturers who specializes in the 2k molding process for medical equipment. We are a trusted supplier for more than 50 medical partners already, and it is still growing. We have a high quality control standard and high injection molding facilities. Visit our website today for twin shot injection molding solutions for any business!