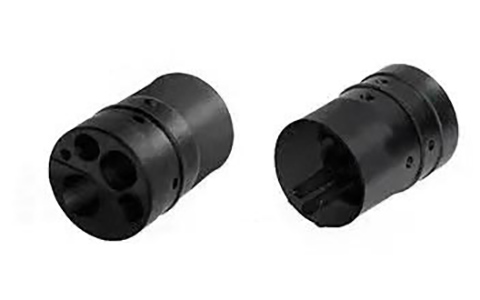
Application of endoscope
Endoscope is a common medical instrument, through the natural orifice of the human body or through the operation of small incision into the human body, the use of the endoscope into the pre-examination of the organ, you can directly peek at the changes in the relevant parts.
Difficulties in realization of endoscope injection molding products
The product has small structure and strict size requirements. In addition, the wall thickness of the product is quite thin, which leads to the difficulty of injection molding and resin filling.
Materials used for injection parts of endoscope
ABS:
low water absorption,
products can be colored into various colors,
small shrinkage,
high dimensional stability,
wide forming temperature range,
with high impact strength and surface hardness.
Good electrical insulation,
not affected by temperature, humidity and frequency,
not affected by water, inorganic salt, alkali, alcohol and hydrocarbon solvents.
High temperature material:
polysulfone has good chemical stability,
high mechanical properties,
good rigidity and excellent dielectric properties,
good dimensional stability of polysulfone,
for general machining and plating,
usually use temperature range is – 100 ℃ ~ 150 ℃,
thermal deformation temperature of 174 ℃,
the creep performance than polycarbonate,
poor weather resistance.
There is also the other high temperature resin such as PEI, PEEK and PPSU etc.
LCP:
LCP molding temperature is high, because of its different varieties, melting temperature in the range of 300~425℃. LCP melt has low viscosity and good fluidity, similar to olefin plastics. LCP has minimal linear expansion coefficient and good dimensional stability.
Notes on injection mold of endoscope
It is necessary to design a reasonable way of injection gate and runner, gate size and shape, to ensure that the product is easy to be injected full and not lack of material;
According to the requirements of product dimension, design reasonable tolerance for mold inserts;
Arrange reasonable mold manufacturing processing, ensure the mold dimension and parts dimension.
When inspection for the mold and inserts, ensure that the measuring method is correct, and ensure they are within tolerance.
When polishing the product, it is necessary to ensure mold and inserts fineness.
To design and manufacture suitable mold venting to prevent air trapping during molding.
Solution in SeaskyMedical
To understand the resin performance is very important for micro molding and thin-wall molding as well as the precise parts. There are few of key factor of the resin listed below affect the injection molding and mold manufacture process.
- Plastic flow property,
- Mold temperature,
- Resin dry temperature and time,
- Injection temperature,
- Clear color or non clear etc.
A few years ago, we design and made a plastic part( 0.2mm thickness, diameter is 4mm and height is 4mm). We did mold trial 9 times and modified the mold 9 times to find a good solution for gate size and venting. For this thin wall and micro parts, there is no solution to guide you on book or a teacher to tell you how to improve. Every year, we faced to new resin and new demand on the market, we invest to study and gather experience. As we do so, we can save cost and time for new customers for product development. Also we know what we can do and which is risky.
You can also review below video to know more for our custom medical injection molding service,