The most well-liked quick manufacturing techniques include injection molding. The quality of the final product is greatly influenced by the injection molding process’s crucial element, the draft angle. Parts without a draft angle in plastic design face the risk of sporting subpar visual finishes and may fold, break, or distort as a result of stress buildup during the molding process brought on by plastic cooling.
Importantly, a lack of airflow could prevent parts from properly ejecting from the mold, damaging both the mold and the pieces. This can become a time and money-consuming interruption. This article will explain an injection molding draft angle and why it’s crucial.
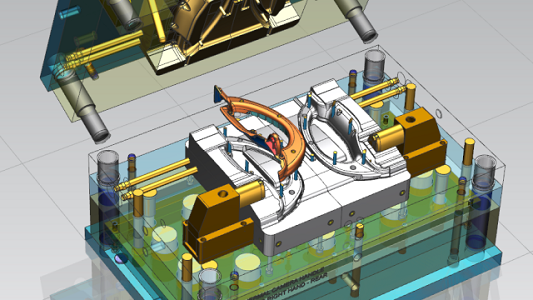
What is Injection Molding Draft Angle?
It is imperative to know what is draft angle injection molding. The slant that is typically imparted to the sidewalls of injection molded parts’ features is referred to as an injection molding draft angle. The injection angles are positioned to run in the same direction as the mold’s draw and separation line. They make it easier to remove the molded parts from the mold.
Draft angle for injection molding helps the design prevent several issues and cut down on production costs. A draft will make it easier for pieces to come out of the mold, which will lead to higher aesthetic finishes and fewer rejected parts. Also, the draft might spare companies from purchasing expensive, complicated ejection arrangements.
Why Draft Angle is Important in Injection Molding Design
After learning what is draft angle in mould, next up is the importance of draft angles. Of all the molding angles, this one is the most crucial. Let’s understand the numerous factors that make it a crucial injection molding variable.
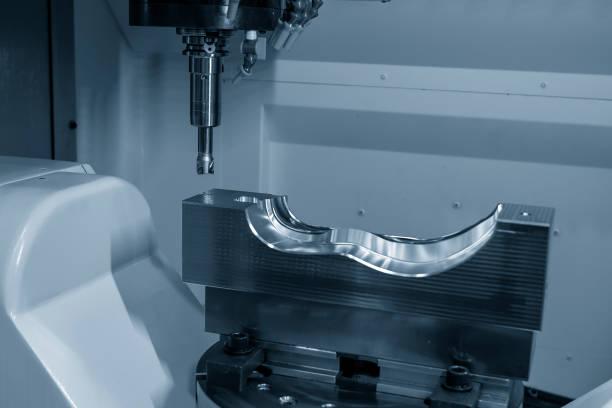
- Avoiding Damage or Deformation of Product
The injection mold draft angle exists primarily because part ejection, a critical stage in the custom plastic injection molding process. The component is in touch with the mold walls just before part ejection. Because of friction during ejection, the part will damage due to the high contact pressure.
The effect of this frictional force should therefore be reduced to the minimum possible. To accomplish this, engineers incorporate a draft into the mold. The part pops out completely and breaks contact with the mold walls as quickly as the ejector pins push it outwards. No friction results from this absence of touch. Friction can result in the deformation of the product.
In the empty space that develops as the part is ejecting, a vacuum may develop if there is no injection molding draft angle by design. The part collapses in on itself due to this vacuum. The draft angle prevents such damage.
- Preventing Flash and Undercuts
Along the drawn line, the mold parts split apart. Deep drawing, flashing, and undercutting are all serious mistakes that can be corrected using this draw line.
A deep draw solves the problem of the part becoming trapped within and to the mold using a mold draft angle. The hazards are decreased with a larger draft angle in injection molding, which helps to lessen the detrimental impacts of a deep draw, such as flash and undercut.
- Reducing Manufacturing Cost
A better surface, less deformation, and fewer deep drawing difficulties are produced by molds with draft angles for plastic parts. Manufacturers spend less on failed components and part finishing as a result. The draft angles also result in substantially lower maintenance expenses.
Moreover, by speeding up the injection molding process, the draft angle also reduces the expenses of manufacturing processes like medical device molding. Rapid cooling processes and part ejection are the results.
- Reducing Cycle Time
The overall cycle time shortens when pieces may be swiftly removed. A draft angle prevents this problem since fighting to remove each unit from the cavity takes time and hinders business operations. Draft angle in plastic design lessens the requirement for unusual, intricate, and pricey ejection arrangements.
- Increasing Product Durability
Lack of draft angles for plastic parts results in significantly increased friction, which is known to cause rougher surfaces on parts. The part’s quality will suffer from too much friction, and the tool life will be reduced, which is more expensive. To remove the part from the mold with the least possible friction against the mold, a draft is used.
So, a reputable medical plastics manufacturing company will incorporate a suitable draft angle to improve the goods’ endurance.
Recommended Draft Angle for Injection Molding Design
The fact is that not all part designs can use a single draft angle. There are several variables at play. There are certain straightforward guidelines that can be implemented to be helpful.
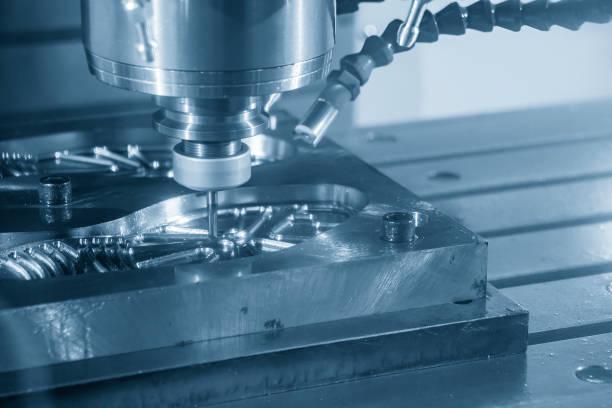
General Angle Range: 1 to 2 Degrees Per Side
Most parts require draft angles of 1 to 2 degrees. Molded items such as injection molding medical equipment with a maximum depth of one to 2 inches are covered by this general guideline. Drafts of 1 degree are sufficient at this size to allow for the simple release of pieces from molds. This aids in preventing some damage to the thermoplastic material during shrinking.
Minimum Angle: No Less Than 0.5 Degrees
For cosmetic reasons, the surface of many injection-molded parts has a leatherette grain or other texture added; nevertheless, based on how dense the texture is put, the draft angle may need to be raised to guarantee the texture won’t be scratched off or ruined during the part ejection process.
Add as much draft angle as needed when constructing a part. 1 degree of draft for every inch of cavity depth—is advised. Nonetheless, it is strongly suggested to keep all vertical faces at least at 0.5 degrees.
With 0.5 degrees of the draft, parts can be designed. Once more, the minimum draft angle for injection molding that is feasible depends on the material, the part shape, and the manufacturer; therefore, before finishing a part with a minimal draft, the plastic injection molding company should be consulted.
Design Considerations for Injection Molding Draft Angle
Draft angle in plastic design assists in preventing expensive and complex ejection settings. These are the design considerations a company needs to make when calculating the draft angle for injection molding.
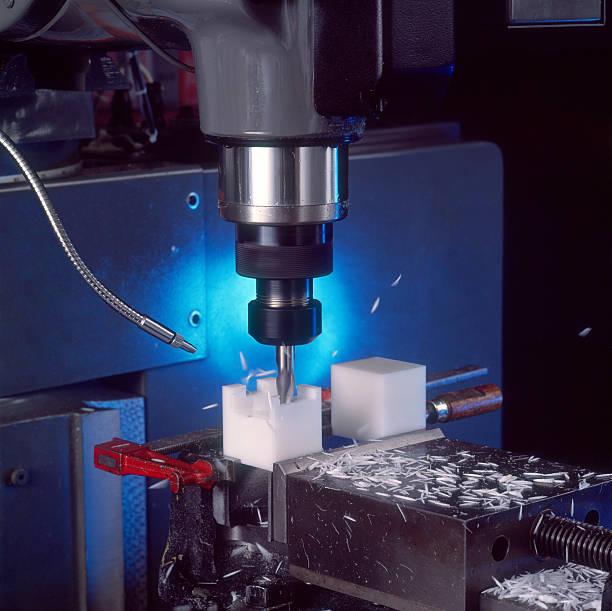
- Material Type and Properties
The kind of material and its characteristics might also affect the injection molding draft angle. For instance, a larger draft angle may be necessary for rigid materials in order to prevent sticking and enable simple ejection from the mold. Conversely, flexible materials can need a smaller draft angle to avoid bending or deformation during ejection.
The needed draft angle may also be impacted by the material’s rate of cooling shrinkage; materials that shrink more rapidly may need a larger draft angle to ensure effective ejection.
- Draft Angle Direction and Degree
When choosing a draft angle for injection molding, consider both the direction and degree of the draft angle. Typically perpendicular to the separating line, the draft angle should be oriented to permit simple component ejection from the mold.
It is important to choose the draft angle’s degree in order to strike a balance between the need for simple ejection and the amount of material needed to form the angle. Indicators including part shape, material qualities, and production needs will determine the precise degree and direction of the draft angle. Products made with injection molding in a clean room should have a proper degree and direction to calculate the correct draft angle.
- Mold and Tool Design
The degree of taper necessary in the draft angle might vary depending on the mold’s design. For instance, a complex geometry mold could need a larger draft angle to allow for simple ejection. The required degree and direction of the draft angle may also depend on the particular design of the tool being used to make it, such as whether lifters or sliders are being employed.
- Part Geometry and Complexity
Larger draft angles may be necessary to enable appropriate ejection from the mold for parts with complex geometries, such as those with extensive undercuts, elaborate detailing, and complex curves. In order to avoid sticking or distortion, parts with significant fluctuations in wall thickness or high aspect ratios would also need larger draft angles.
For some designs necessitating the application of draft angles in several directions, the intricacy of the part might also have an impact on the precise direction of the required draft angle. Designers can choose the right degree and direction of the draft angle necessary to enable effective and economical injection molding manufacturing by carefully evaluating the geometry and complexity of the part.
Seaskymedical: Focus on Ideal Draft Angle in Injection Molding
Seaskymedical is an expert plastic injection molding company. We offer excellent mold-making and production services, as well as draft angles that are incredibly precise in their manufacturing of molding products. We offer a full one-stop tooling solution because of their cutting-edge technologies, efficient manufacturing processes, and expert management.
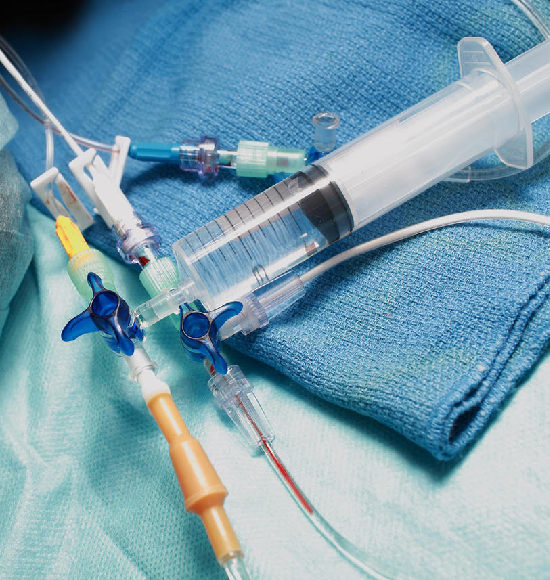
Seaskymedical is one of the best injection molding businesses that could successfully implement draft angles thanks to its more than 20 years of injection molding experience, modern injection molding equipment, a huge workshop, and skilled people. We have provided the healthcare sector with low-risk, economical solutions. In addition, we provide clients with thorough and knowledgeable support for the duration of the entire project.
Modern molding tools, a sufficient supply of materials of the highest medical quality, an ISO 8 cleanroom, and efficient production lines are all present at Seaskymedical. Before being given to the client, every injection-molded product is subject to a number of quality assurance tests, including a draft angle accuracy test.
Conclusion
Crucial elements of well-designed parts include injection molding draft angle. They make sure that production procedures are efficient and of a high standard. An excessive number of parts may be discarded if the draft angle is ignored. Mold damage is another consequence.
Be updated on injection molding best practices at all times for the greatest results. Draft angle integration into injection molding is one of them. Welcom to contact Seaskymedical to get exceptional injection molding services.