Medical parts are not only used by doctors in hospitals or specialists in other healthcare institutions. They are also used across several sectors, including clinics, laboratories, research institutes, and even schools. Thus, medical molding companies are always engaged to manufacture bulk medical parts to cater to all these sectors. And to make large production without compromising on quality within a fast period of time, plastic injection molding process is used. Plastic is used because its processing is fast, hygienic, disposable, and easy to work with.
In this post, we will disclose more reasons why the plastic injection molding process is preferred, including the various medical components made from this process, the types of plastic materials used in the making, and so many more.
Stay tuned!
Medical Device Injection Molding Overview
Injection molding is a fast and cost-effective production technique used to make plastic parts in large volumes. Medical device injection molding, on the other hand, is the process of making these plastic parts for application in the medical industry.
Production of medical plastic products is keenly monitored as there are several standards and regulations that must be followed. These products must be finely manufactured to be sterile and usable inside and outside the human body without causing any havoc.
Benefits of Medical Device Injection Molding
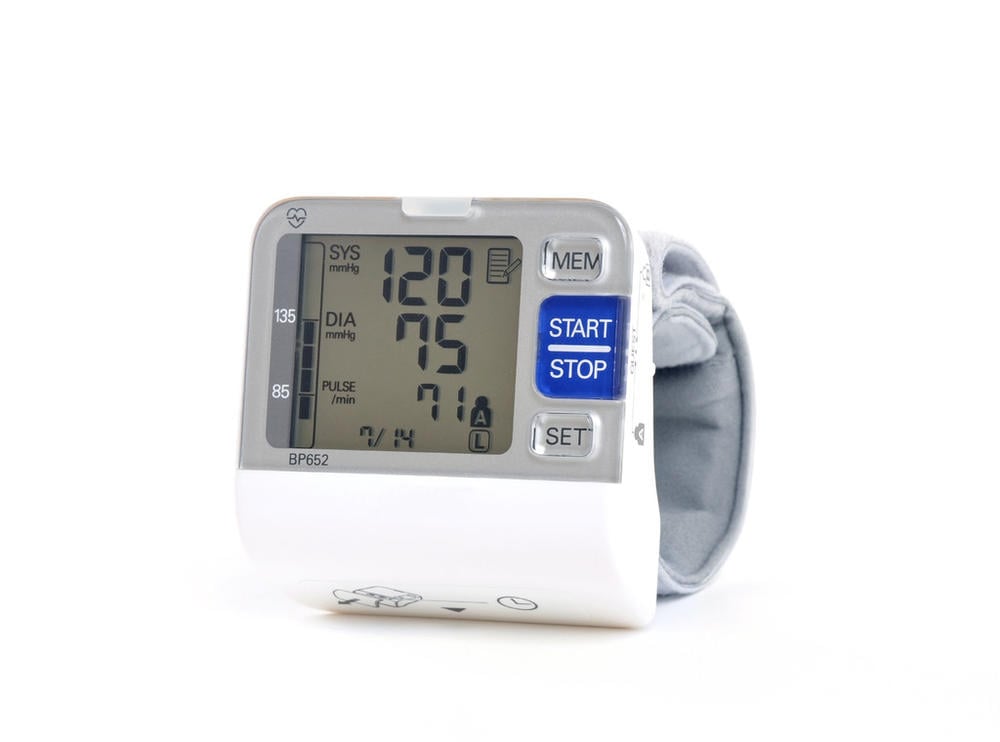
With the smooth and seamless operation of the medical injection molding process, there are numerous advantages the process offers. Asides the fact that it results in better hygiene and saves more lives, here are some other benefits.
- Wide Variety of Material Selection: Plastic injection molding arguably has the broadest material selections of any manufacturing process. This is one great benefit that medical plastic manufacturers enjoy as they are able to make different specifications of healthcare equipment, thereby providing various solutions for patients.
Although the standards of medical devices limit the material choice, there are still a wide range of options to choose from. Health tools require precise materials with exceptional properties for optimal functionality. These materials must also have certain features like ease of handling, heat resistance, hit resistance, chemical resistance, etc. Amongst the popularly used materials are Polypropylene (PP), Polyethylene (PE), Polystyrene (PS), and Polyetheretherketone (PEEK).
- Fast Production Process: The time taken for injection molding is very fast compared to other manufacturing processes. This is why the process is majorly used in healthcare institutions as it can be used to make devices faster in case of out of stock and emergency occurrences. For example, when a patient is involved in an accident and a knee brace is needed. With this process, the knee brace will be made quickly without putting the patient’s life at risk.
Also, some health tools, such as syringes and test tubes are often needed in large numbers. Using other manufacturing techniques would be slow, and in the medical industry, time is vital. With plastic injection molding, bulk production can be made within a lesser timeframe.
- Cost-efficiency: Medical equipment tends to be pricey to make, but plastic injection molding makes them cost-effective. This is because production is usually done in large quantities and it requires injection molding die made from strong steel that can be used for repeated creation. With this, high volume of medical parts are produced without incurring extra cost other than the initial tooling expenses. And plastic, which is the material used, is very easy to source.
Thus, plastic injection mold offers quality while maximizing resources. The strength and continuity of the molding die reduces future rework costs. Also, it reduces manpower as the process is automated, meaning that much can be achieved with lesser staff. The production of simple devices like tubes, containers, and syringes are made with injection molding because it offers complex shapes in large quantities with economical cost.
- Durability: Health tools need to be strong because they are stored in harsh conditions. They are either in cold storage or a warm state. So, these tools must be manufactured with tough materials that can endure unconducive weather. They also need to be hit-resistant.
A notable fact about plastic medical injection molded components is that they are ruggedly durable. Materials used provide superior strength and resistance to adverse environments and applications, making the devices produced to be able to withstand heat, blunt force, and vibration without any occurrence of cracks or breakages. In fact, when they are put under high pressure, high temperature, or sterilization in an autoclave, they don’t bow to the heat.
- Exceptional Accuracy: Medical devices require exceptional precision as a millimeter or micron error in the tight tolerance, size, weight, length, breadth, or any part of the composition can lead to an unfortunate occurrence. But with the medical injection molding process, accuracy is guaranteed. Even in bulk production, precision is not compromised.
- Clean Room Production: According to the FDA and other regulatory standards, medical injection molding in clean room is mandatory. The manufacturing process must be carried out in a sterilized factory that’s void of contaminants and bacteria. This is done to prevent the medical equipment from complicating patients’ illnesses. In fact, the materials utilized easily withstand invasion of germs, meaning that they don’t need much sterilization to be safe.
- Lightweight: As opposed to other materials like metal and wood that are heavy, medical device injection molding is made of plastic, which is light and easy to use. This allows healthcare practitioners to be able to control the devices freely and this reduces the chances of error during operation.
- Customization: Medical devices are not like other equipment. They require exact sizes, matter, and conditions. Every medical device is made for a specific purpose. So, only a method like plastic injection molding that permits flexibility and customization can be fully used. The manufacturing process gives leeway to alter the medical parts style to make unique products, such as restyling lab tools cases and surgical wearables to fit each medical practitioner.
Injection molding can be used to make any shape that’s almost impossible to form. The flexibility of the process permits the recycling and re-molding of the device. No matter how difficult the device geometry is, with this manufacturing process the device can be judiciously fabricated without having a fault.
- Compliance with Basic Standards: Health is very important, so there are basic standards that every tool used for medical operation must comply with before use. These standards are set by the Food and Drug Administration (FDA) and International Standard Organization (ISO). These basic standards test the usability and quality of the devices. If the devices don’t comply with the standards, they won’t be approved for use.
Medical components manufacturing with other processes other than injection molding might not give the desired result, resulting in the disapproval of the components. Injection molding process has multiple checks and stringent quality control stages that ensure full adherence to these standards.
Plastic Injection Molding Products in the Medical Industry
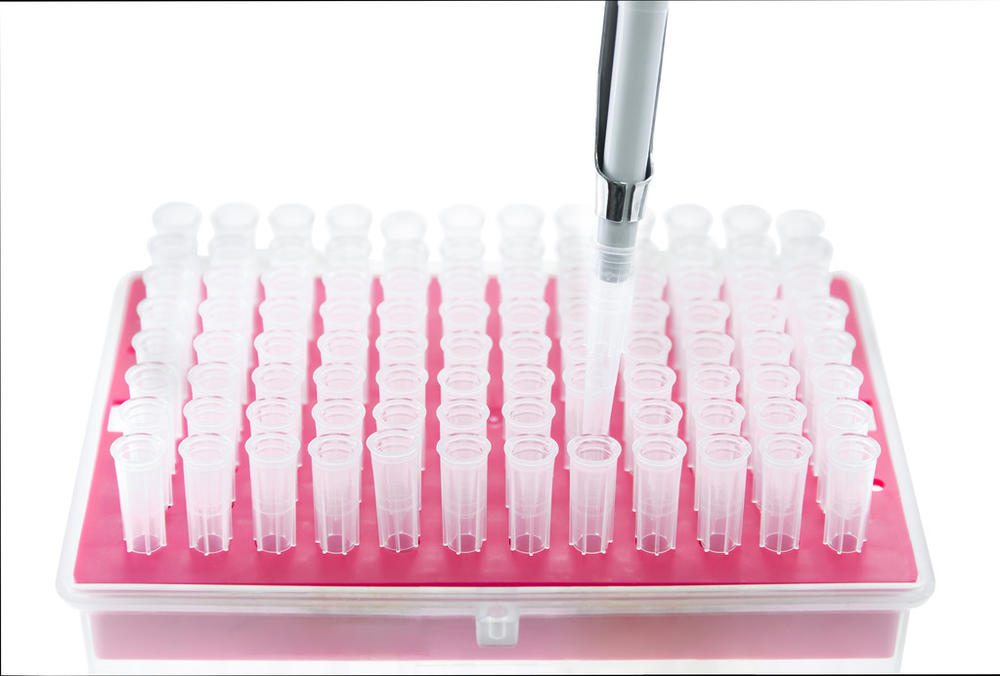
Plastic is best preferred for making medical components because of the various benefits it provides, such as lightweight, safety, production in high volume, etc. The applications of the medical plastic injection molding devices is almost limitless.
- Lab tools: Many lab tools need casings that are strong, protective, and transparent. With plastic injection molding, the perfect storage can be provided, protecting the lab tools from harm, unwanted access, dust, while making them transparent for easy location.
- Test tubes and syringes: Doctors and health centers commonly use tubes and syringes to house fluids, as well as inject drugs and vaccines into the body. The body of these parts are made using injection molding.
- Surgical devices: Surgery operations demand the use of many tools, which can be made with plastic injection. Tools like catheters, insulin pens, and IV tubes are made from this process.
- Implants: Health centers use implants that are made with strong and wear-resistant plastics. Artificial heart implants, knee implants, and even some breast implants are made using plastic injection molding.
- Orthopedics: To fix deformities in human bones, orthopedic tools are the go-to equipment. These tools are designed to fit accurately and most of them are made with plastic injection molding. Some of these tools are knee braces, hip support, wrist support, and back supports.
Other medical devices that are made via plastic injection molding include:
- Luer fitting
- Pipette tip
- IV set
- Prosthetics
- Lab equipment
- 96 deep well plate
- Beakers
- Surgical blades
- Peacemaker parts
- Dental tools
- Instrument handles
- Suture delivery devices
Materials Used in Making Plastic Injection Molding Medical Parts
Plastic materials have shown their utility and quality in a variety of medical products and have already received FDA certification. The different injection molding plastic resins are vast and can be specifically formulated for various healthcare applications. These resins don’t harbor pathogens and can stand up to several sterilization processes.
- Polypropylene (PP)
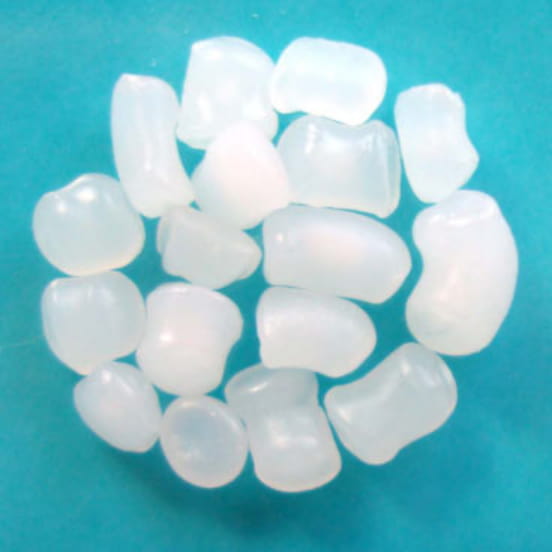
This plastic resin is known for its ruggedness and durability, making it one of the most used materials in the medical industry. PP contains strong chemical bonds that makes it appropriate for producing medical tools like test tubes and beakers. Having high resistance to heat and radiation over a long time, it’s best for items that require repeated sterilization through autoclave.
- Polyethylene (PE)
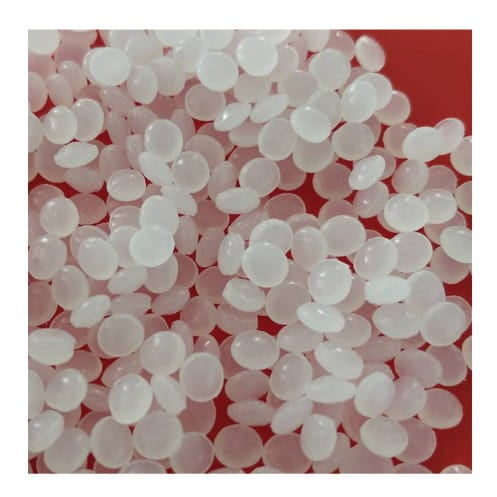
This plastic resin is arguably the main component of the thermoplastic polymer family used for numerous industrial and commercial parts, while offering varying levels of rigidity. It comes in different folds with different durability levels, which include LDPE and HDPE. The material has high molecular weight and is part of most prosthetics for the hip, leg, and other joints, as well as other devices that can be worn thanks to its appearance, smoothness, and strength.
PE is both cost-effective and durable, but it’s a bad choice for hot environments as it can deform and change shape under extreme heat. Also, it cannot be sterilized with an autoclave.
- Polystyrene (PS)
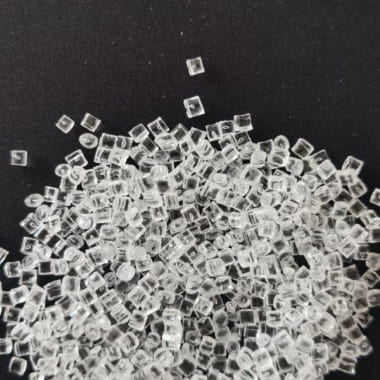
This is a tough plastic material that has almost no elasticity; it’s not flexible but exhibits an extremely high level of impact resistance and machinability. It’s colorless but naturally transparent. Some custom plastic injection molders will add a pigment to offer color variation. Popularly used on customizable surfaces, PS has great dimensional stability and works fine on aesthetics.
- Polyetheretherketone (PEEK)
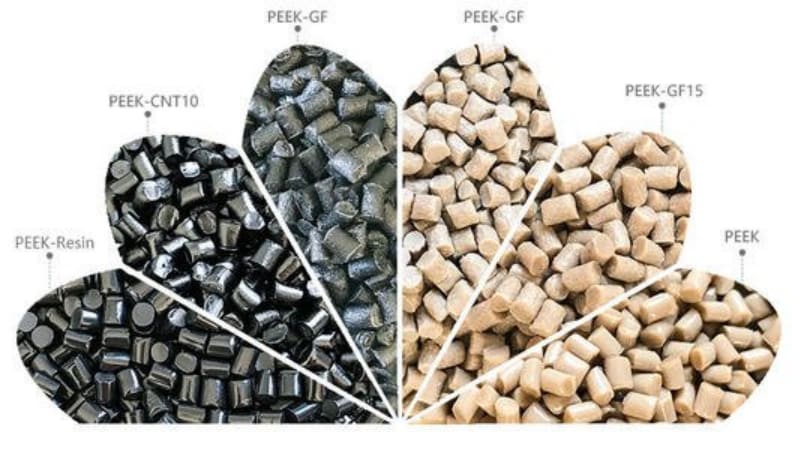
This is a thermoplastic material with high performance and exceptional mechanical properties. It’s known for its high-grade resistance to wear, radiation, chemical, crack, and thermal degradation. PEEK is a popular exotic medical-grade plastic that can be sterilized via autoclave and it’s often used in environments with organic and aqueous elements.
- Silicone
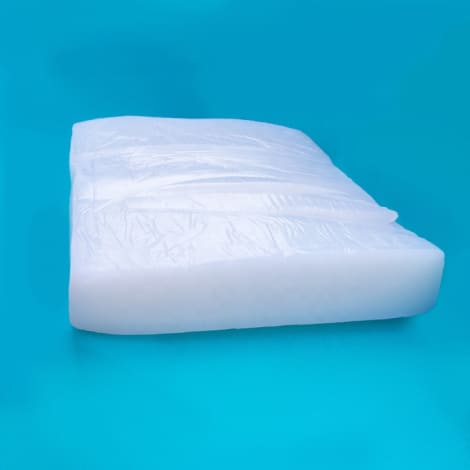
This is a go-to material when flexible medical devices are to be produced. It possesses the capability to make the devices greatly durable and biocompatible than other materials. Silicone is very affordable and reduces costs in high-volume productions.
- Polycarbonate (PC)
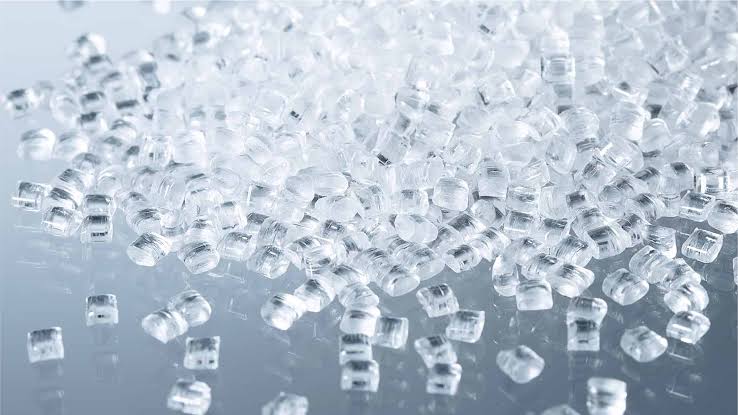
A tensile, flexural strength, and shear medical-grade plastic that is usually transparent and often used for manufacturing syringes, medical tubing, centrifugal force separators, blood filter housings, and other health tools that require visibility. PC offers high heat resistance, extensive impact resistance, and low moisture absorption.
Things to Consider When Selecting Materials for Medical Plastic Molding
Medical devices are crucial tools that have to be manufactured appropriately and in accordance to health regulations as they determine the survivor of human life. Each material has unique properties that determine their performance with applications and operating environment. So, before selecting the material to use for your application, here are the factors to consider to know if the medical device produced will be functional.
- Properties of the Materials: As highlighted in the previous section, each plastic material has its unique properties. While some plastic resins can be used to make transparent tools, others cannot. So, it’s essential that you check out and confirm the properties of each material before choosing the best for your application.
- FDA Regulations: For medical components production, FDA standards are one of the major requirements to consider. In fact, if the medical molded part does not adhere to FDA regulations, it’s unsuitable to be used for health purposes.
The standards involved include sterility and cleanliness, which is why injection molding in a clean room is essential. In all production stages, make sure all inputs conform or surpass the laid down standards. Also, for devices to be approved as medical-grade, the production factory must comply with the necessary standards.
- ISO Certification and Compliance: Another important health organizational standard that must be adhered to is the ISO. At a minimum, factory manufacturing medical devices must comply with ISO 13485 and Class I, II, or III depending on the devices produced.
Additional standards like ISO 10993 and biocompatibility can be made compulsory in some cases.
- Withstand Sterilization Processes: All components that come in contact with the human body must be germ-free. Preferred materials are those that can go through autoclave sterilization without deforming.
Also, antimicrobial additives can be applied on the materials during the injection molding process to prevent the growth of fungus, algae, and other microbes. If this is not done, the injection molded medical components can promote microbial growth, which will require frequent sanitation that can end up reducing the component’s lifespan.
- Durability and Strength: To avoid the injection molded medical device from breaking or cracking, it’s essential that you consider the strength and durability of the material used. Just as mentioned in the previous section, plastic resins have different levels of strength, so it’s important that the material used for a device provides the strength needed for the application. Plastic injection molding materials should be strong, tough, and function effectively throughout their service life.
- Operating Environment: The ability to withstand harsh conditions is a crucial factor to consider for molding materials. They must be strong and tough so that they won’t degrade when exposed to heat, corrosives, liquid, vibrations, and other coercive elements. Failing to put the environment where the molded part will be operating under consideration can cause faster degradation or total failure of the component.
- Molding Method: Injection molding, insert molding, overmolding, and micro molding are some of the popular methods used in making medical devices. But not all plastic materials are compatible with all these methods. It is crucial to be sure of the manufacturing method that will be used before selecting the material.
Injection Molding Technology to Manufacture Medical Plastic Products
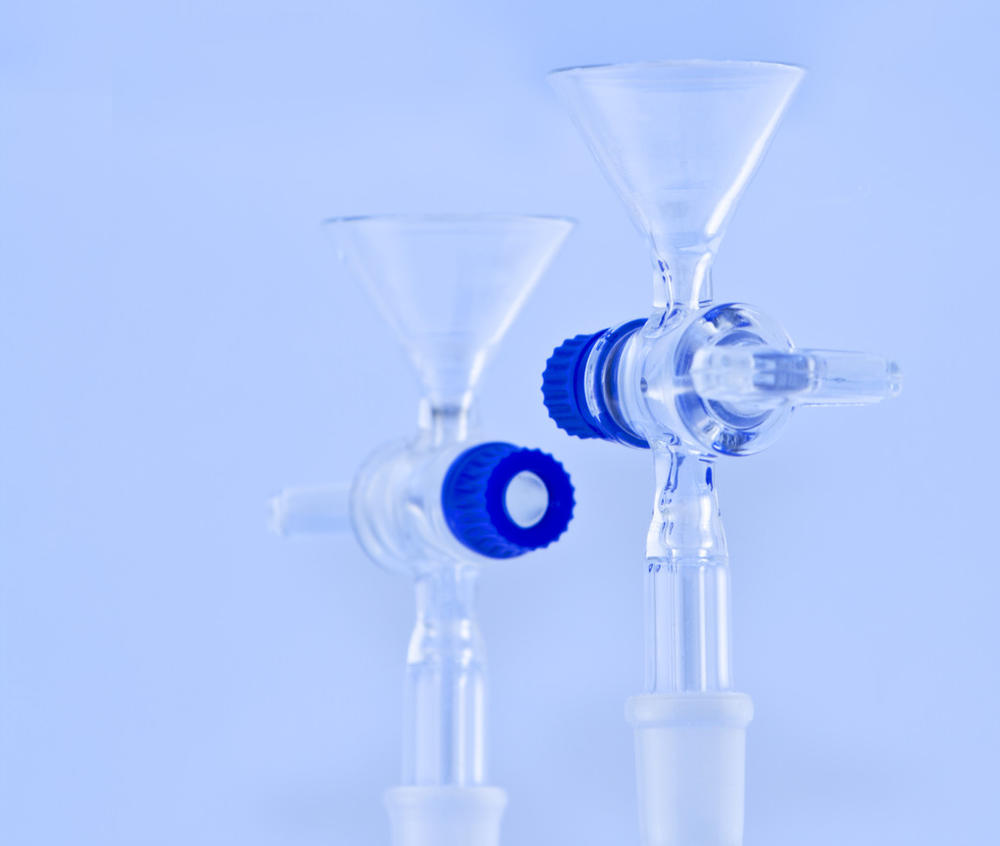
Other than the normal injection molding, there are some other molding technological processes that are used to manufacture medical plastic parts. They are:
- Insert Molding: Involves encapsulating an already molded part (commonly called an INSERT) with freshly injected molten plastic. This helps to form a strong bond between the two materials. Most inserts are metal and they include threaded nuts, knobs, sleeves, blades, bushings, and screwdrivers. With the plastic material molded around them, they will be easier to grip and comfortable to use without slippering or slowing work rate.
- Overmolding: Involves the molding of several plastic resin together to form a strong and tough device. Firstly, a chosen plastic material will be injection molded to form the substrate. Then, the other plastic resins will be heated to their molten state one after the other and injection molded in, on, or around the substrate as the case may be. As the materials cool, they bond together, and form a strong and durable part.
- Micro Molding: An injection molding process for the manufacture of plastic parts that are extremely small, require high precision with micron tolerance (usually 10 to 100 microns). It’s used for shaping and forming plastic parts that are often less than a gram in weight (0.1 to 1 gram).
- 2K Injection Molding: A manufacturing process in which two materials are processed in one plastic part using a 2K injection molding machine. The selection of material is the most important factor. Both materials must be biocompatible.
- Clean Room Injection Molding: A process for manufacturing medical devices that are contaminant-free. Clean room injection molding ensures that production is made in compliance with customers’ specifications while adhering strictly to regulatory standards.
Medical Plastic Injection Molding Process
The step-by-step process involved in carrying out medical plastic injection molding is pretty simple and straightforward. Choose the right material(s) for your medical tool application then follow these steps:
- Medical Parts Design and Engineering: Firstly, discuss and be certain of the specifications of the medical part you want to produce. Then, specialized engineers should design the desired medical part, including all the specifications demanded.
- Mold Tooling Custom and Making: A corresponding mold to the medical part designed should be formed. The tooling of the mold is crucial. Ensure you use strong metal that won’t get damaged due to the temperature and harsh conditions it will be exposed to. Also, the mold must be fabricated to be tough and durable as it will be used to make multiple parts.
- 3D Prototype: Using a three-dimensional computer aided design, make a prototype of the medical part. With this, you will be able to know if the part and mold designed are functional as it will display the weight, geometry, and other details. And if it’s not good enough, make necessary changes and conduct another 3D prototyping.
- CNC Machining: Using a CNC machine, you can make perfect modification to the irregularities in the medical part prototype. With the computerized control aid, the machine will remove layers and wrong dimensions, providing you with the perfect medical part and mold design desired.
- Injection Molding: After the medical part and mold design are completed, heat the plastic material to change to a molten state. Inject the molten plastic into the mold, let it cool, solidify, and form into the desired medical shape.
Seaskymedical Medical Device Injection Molding Service
Amongst all the plastic molding companies on the market, Seaskymedical is the leading professional with a track record of offering reliable medical device injection molding services. Having over 10 years of experience in the medical device plastic injection molding industry, Seaskymedical has provided many healthcare institutions with one-stop service of making high-quality medical tools that are made from suitable materials and also comply with regulatory standards like the FDA and ISO.
And all these manufacturing processes are carried out in a fully-equipped Class 8 clean room factory that ensures the production of contaminant-free health equipment. To get the best plastic medical device injection molding service, don’t fail to contact us. We are here to help with all you need.