Injection moulding is an exceedingly efficient and cost-effective manufacturing process requiring much precision and skill. It is a widely used manufacturing process in various industries, including automotive, electronics, medical devices, and consumer goods.
This versatile technique can be used to create parts and components of varying complexity out of many different types of material, that is why there are many plastic injection manufacturer today across the globe.
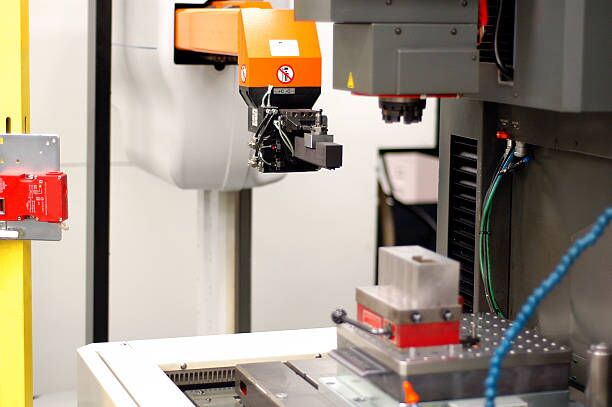
In order to produce the best possible results, it is important for manufacturers to take into account the different type of gate that can be used in injection moulding. Exploring these nine types of gates more closely, it can help businesses optimize their injection molding processes and achieve better results.
What is Injection Molding Gate?
Injection molding is a production method in which the injection of molten plastic into a mold cavity to create a solid plastic component. The process involves several critical components, including the injection unit, the mold, and the gate. The gate is a small opening through which the molten plastic enters the mold cavity.
It is a crucial component of the injection molding process as it determines the flow rate, pressure, and cooling of the molten plastic, which affects the quality and properties of the final product.
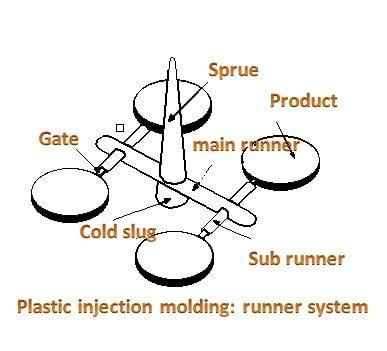
The primary purpose of an injection molding gate is to act as a funnel or funnel-shaped opening that controls the flow of molten plastic from the nozzle tip of an injection molding machine into the mold cavity. It also helps minimize air entrapment in the molten plastic as it enters the cavity, which can lead to surface defects on the finished product.
There are several types of gates in injection molding available, and choosing the appropriate one depends on various factors such as the part design, material, and production requirements. The size and location of the gate are also critical factors in determining the success of the injection molding process.
A gate that is too small or located in an inappropriate position can cause several issues such as part deformation, warpage, and poor surface finish. Similarly, a gate that is too large can result in excessive material waste and longer cycle times.
In addition to its role in controlling the flow of plastic, the gate also serves as a point of separation between the runner system and the molded part. The runner system is a network of channels that distributes the molten plastic from the injection unit to the mold cavity. Once the part is formed, the runner system is separated from the part at the gate, and the remaining material is typically recycled or discarded.
9 Types of Gates in Injection Molding
There are several injection molding gate types available in the market today, each with its unique features and advantages. Here are the nine types of gates commonly used in injection molding.
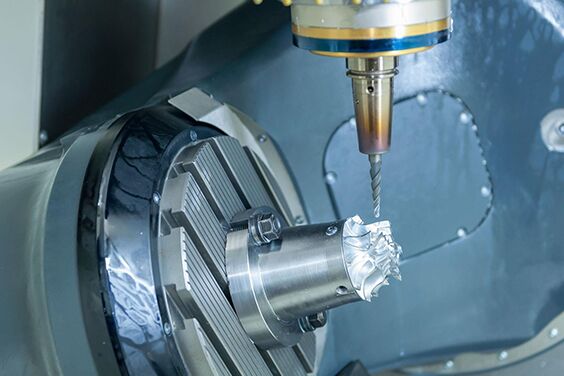
Direct or Sprue Gates
Direct or sprue gates are the most common type of gate used in injection molding. They are typically used for large parts or parts that require a high volume of material. In this type of gate, the molten plastic is injected directly into the center of the mold cavity through a large-diameter opening. The sprue gate is then removed from the part during post-processing.
Direct or sprue gates are easy to design and implement, but they can leave a visible mark on the surface of the part, known as a gate mark.
Edge Gates
Edge gates are one of the gate types injection molding and it is also known as a tab gate or a film gate. Edge gates are commonly used for thin-walled parts or parts with delicate features, as they leave behind a smaller gate mark than other types of gates. They are typically used for small or thin-walled parts, where the gate mark is less visible.
Edge gates are usually designed to minimize the material flow distance, resulting in faster cycle times and reduced waste. However, they can also create weld lines or knit lines in the part where the flow fronts meet.
Submarine Gates
Submarine gates are another injection molding types of gate that is located below the surface of the part, typically on the underside or back of the part. It allows the molten plastic to flow into the cavity from the bottom, which can help to reduce the visible gate marks on the part. Submarine gates are commonly used for parts with thick walls or parts that require a high level of aesthetic finish, such as automotive parts or electronic housings.
However, they can also create weld lines or knit lines in the part where the flow fronts meet. Submarine gates are typically more difficult to design and require special considerations to ensure proper filling of the part.
Cashew Gates
This type of gate injection molding is named after its shape, which resembles a cashew nut. It is also known as a banana gate or an extended gate. The cashew gate is a variation of the edge gate and is used to gate thin-walled or delicate parts that require a small gate mark. The gate is located at the edge of the part and is extended along the surface of the part, which allows the molten plastic to flow more evenly into the cavity.
The cashew gate is typically used for cosmetic parts, such as lenses or covers, as it leaves a small gate mark that is less visible than other types of gates. However, it can also create weld lines or knit lines in the part where the flow fronts meet. The cashew gate requires precise design and molding considerations to ensure proper filling of the part and to prevent part defects.
Diaphragm Gates
Diaphragm gate uses a diaphragm valve to regulate the flow of molten plastic into the cavity. The diaphragm is typically made of a flexible material, such as rubber or silicone, and is held in place by a pin that extends into the cavity. When the pin retracts, the diaphragm opens, allowing the plastic to flow into the cavity. When the pin extends, the diaphragm closes, preventing any additional plastic from entering the cavity.
Diaphragm gates are commonly used for parts with complex geometries or parts that require precise control over the flow of plastic, as they allow for greater control over the filling process. However, they can be more complex and expensive to implement than other types of gates in injection molding.
Hot Runner Valve Gates
This is one of the injection molding gate types that use a valve pin to control the passage of molten plastic into the cavity. The valve pin is typically made of durable material, such as steel or ceramic, and is controlled by a hydraulic or pneumatic system. When the valve is open, the plastic flows into the cavity. When the valve is closed, it cuts off the flow of plastic, preventing any additional material from entering the cavity.
Hot runner valve gates are commonly used for high-precision parts or parts with intricate geometries, as they allow for precise control over the flow of plastic and can help to reduce the occurrence of part defects. It can be more expensive and complex to implement than other types of gates, but they offer greater flexibility and control over the molding process.
Hot Runner Thermal Gates
Hot runner thermal gates are a type of gate that uses a heated manifold to control the flow of molten plastic. The manifold is typically made of a heat-resistant material such as aluminum or copper and is placed between the nozzle and the mold cavity.
The plastic flows through the manifold, which is warmed to maintain the molten state of the plastic. One of its main advantages is that they allow for precise control over the temperature and flow of the molten plastic. This can result in parts that have a high level of accuracy and consistency.
However, hot runner thermal gate systems can be more complex and expensive to implement than other types of gates. The manifold and associated components require precise injection mold gate design and careful construction to ensure that the plastic is distributed correctly and that the system operates efficiently.
Fan Gates
Fan gates uses a small, flat gate that is attached to the part at one end, with the other end extending into the mold cavity. The plastic flows through the gate and into the cavity, filling the part from the side. Fan gates are commonly used for parts that require a clean, finished appearance on one side, as the gate mark can be located on the side of the part that will not be visible or on a separate runner that can be easily removed.
One of the advantages of fan gates is that they can help to reduce the occurrence of cosmetic defects on the part. Since the gate mark is located on a non-visible part of the part or on a separate runner, it does not affect the overall appearance of the part. However, one of the limitations of fan gates is that they can result in the uneven filling of the cavity, particularly for parts with complex geometries.
Pin Gates
Pin gates are types of injection molding gate that uses a small-diameter pin to control the flow of molten plastic. The gate is typically located at the edge of the part, and the plastic flows through the narrow opening of the pin gate, resulting in less waste and faster cycle times. Pin gates are commonly used for parts that have thin walls or require a high level of precision.
One of the advantages of pin gates is that they can result in a clean, finished appearance on the part. Since the gate mark is small and located in a non-visible area, it does not affect the overall appearance of the part. Additionally, pin gates can be useful for parts with small features or thin walls, as they allow for a precise flow of plastic into the cavity, reducing the risk of sink marks or other defects.
The Importance of Gate Type and Gate Placement
The type and location of the gate play a crucial role in determining the quality and consistency of the final injection-molded product. Different types of gate offer various advantages and disadvantages, depending on the specific requirements of the product. Similarly, the location of the gate can affect the flow of molten plastic, filling pattern, and warpage of the part.
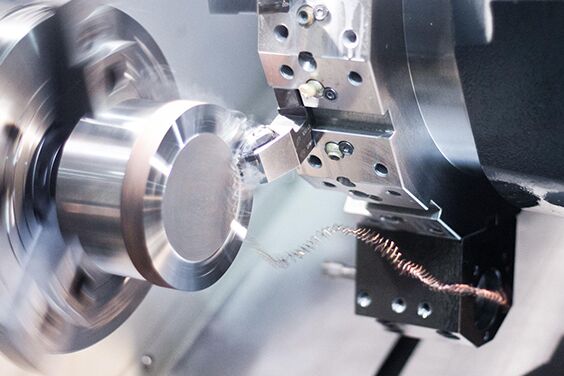
For Injection Mold Gate Type
Choosing the appropriate gate type is crucial in injection molding as it can affect various factors such as part quality, cycle time, and tool life. Selecting the correct gate type, such as edge, submarine, pin, or hot runner, is essential based on the specific requirements of the part being produced.
The proper selection of gate types can significantly improve the quality of the final product. For example, the gate type can ensure consistent filling, packing, and cooling of the mold cavity, resulting in a finished product with better surface finish and dimensional accuracy.
In addition, the proper selection of gate types can reduce cycle time by optimizing the flow of molten plastic, thus minimizing the need for additional post-processing operations. Moreover, gate type can impact tool life, as an incorrect gate type can cause excessive wear and tear on the mold, leading to reduced tool longevity.
For Gate Location in Injection Molding
The location of the gate also plays a critical role in the success of the injection molding process. The gate location affects the flow of molten plastic, filling pattern, and part warpage. For example, a gate located at the thickest part of the product can result in uneven filling, while a gate located too close to the edge can cause a warpage.
On the other hand, a gate located at the center of the product can result in uniform filling and minimal warpage. The gate location also depends on the specific requirements of the product, such as surface finish, part strength, and production volume. In some cases, multiple gates may be required to ensure uniform filling and prevent warpage.
Overall, choosing the right gate types of injection molding and gate location is essential for ensuring a successful injection molding process. A thorough understanding of the product requirements and material properties can help determine the optimal gate type and gate location for a specific product, resulting in high-quality, consistent products that meet or exceed customer expectations.
Key Points to Consider When Choosing Injection Molding Gate
Choosing the right injection molding gate is a critical step in the manufacturing process. It is important to consider various factors to assure that the final product meets or exceeds customer expectations. Here are some essential considerations when selecting an injection molding gate.
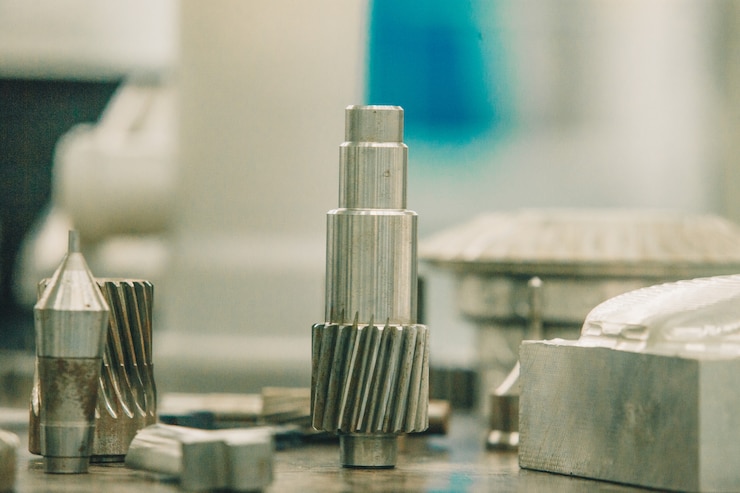
Suitable Gate Placement
The placement of the gate is a critical factor in injection molding, and it can significantly impact the final product’s quality and appearance. Choosing a suitable gate placement is crucial for achieving a uniform filling of the mold cavity and reducing the risk of defects such as warpage, sink marks, and voids.
The ideal gate placement should allow for even distribution of the molten plastic throughout the mold cavity. The gate should be placed in a location that promotes uniform filling, packing, and cooling of the part. A well-placed gate injection molding can ensure that the molten plastic reaches all areas of the mold cavity, resulting in a final product with consistent dimensions and surface finish.
The gate placement should also consider the part’s geometry and design. For instance, parts with complex geometries may require multiple gates to ensure proper filling and avoid any defects. Similarly, parts with thin walls or small features may require gates in specific locations to prevent warpage or sink marks.
In addition to functional considerations, gate placement should also take into account any aesthetic requirements. The gate location should be chosen to avoid visible gate marks or weld lines on the final product. The gate should be placed in a location that minimizes any visible defects or blemishes on the surface of the part.
Gates of Adequate Size
A gate that is too small or too large can significantly affect the quality and cost-effectiveness of the production process. If the gate dimension is too small, it may not allow enough material to flow into the mold cavity, resulting in incomplete parts or defects. This can lead to issues such as poor dimensional accuracy, warping, and sink marks.
On the other hand, if the gate size is too large, it may create excessive waste and increase production costs. A large gate will result in more material being used than necessary, leading to increased scrap and material costs. Choosing an injection molding gate of adequate size is essential to optimize the production process and achieve the desired results.
The gate size should be determined based on the part’s specific needs, including its size, complexity, and design. It is also vital to consider the type of plastic material being used, as different materials may require different gate sizes.
Preferred Part Shape and Finish
The shape and finish of the part should also be considered when choosing a gate. Different gate types offer varying levels of control over the flow of molten plastic, which can affect the final part’s shape and surface finish. For example, a direct gate may be suitable for a simple, uniform part with a rough surface finish, while a hot runner valve gate may be better for a complex part with a smooth, glossy finish.
On the other hand, a hot runner valve gate is a more complex gate type that allows for precise control over the flow of molten plastic into the mold cavity. This type of gate is suitable for complex parts with intricate geometries and requires a high-quality surface finish. The valve gate provides excellent control over the flow of molten plastic, which results in a smooth and glossy surface finish.
Number of Injection Molding Gates
The number of gates required for injection molding is an important consideration as it can affect the part’s quality, production time, and cost. The optimal number of gates depends on several factors, including the part’s design, size, and geometry, as well as the material properties and production requirements.
In general, an injection mold gate design and geometry will dictate the number and location of gates required. Parts with complex shapes or thin walls may require multiple gates to ensure even filling and minimize defects such as warping, sink marks, and voids. In contrast, parts with simpler geometries may require only one gate to achieve adequate filling.
Seaskymedical Offers High-Class Plastic Injection Molding Services
Seaskymedical is a leading provider of high-class plastic injection molding services and one of the most reputable medical plastic manufacturers across the world. With years of experience and expertise, they have established themselves as a trusted partner for customers in the medical, automotive, and consumer electronics industries.
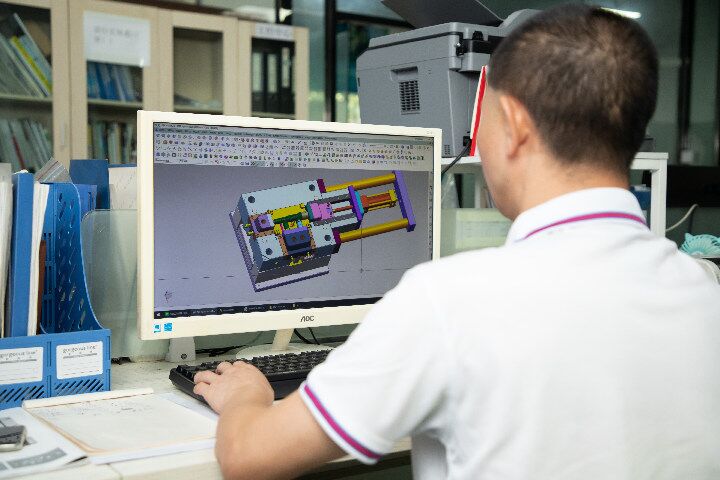
Seaskymedical offers a wide range of types of injection molding services, including custom injection molding, insert molding, and clean room injection moulding. Our state-of-the-art facilities, cutting-edge technology, and skilled team of professionals enable them to deliver high-quality products that meet or exceed customer expectations.
We are also committed to providing exceptional customer service, with a focus on responsiveness, flexibility, and collaboration. We also offer custom plastic injection molding. We work closely with their customers to understand our specific needs and requirements and provide tailored solutions to meet those needs.
In addition to injection molding services, Seaskymedical also offers value-added services such as design assistance, prototyping, and assembly. Our comprehensive approach enables customers to streamline their supply chain and reduce costs while maintaining high-quality standards.
Overall, Seaskymedical is a reliable and trusted partner for customers seeking high-quality plastic injection molding services. Our commitment to quality, customer service, and innovation sets us apart from our competitors and makes us a go-to partner for customers in a wide range of industries.
Conclusion
Injection moulding is a highly versatile and cost-effective manufacturing process that is ideal for producing high-quality parts of varying complexity. Understanding the different types of gates in injection molding and their characteristics can help businesses optimize their injection moulding processes and achieve better results.
There are injection molding companies today that offer injection molding processes. Seaskymedical is a leading provider of high-class plastic injection molding services for customers in various industries such as medical device injection molding. We offer comprehensive solutions to meet customers’ needs with attention to quality, customer service and innovation. Visit our website today for any types of injection molding that any business might need!